【間違いだらけの】生産管理|生産性向上 段取回数をどんどん増やせ
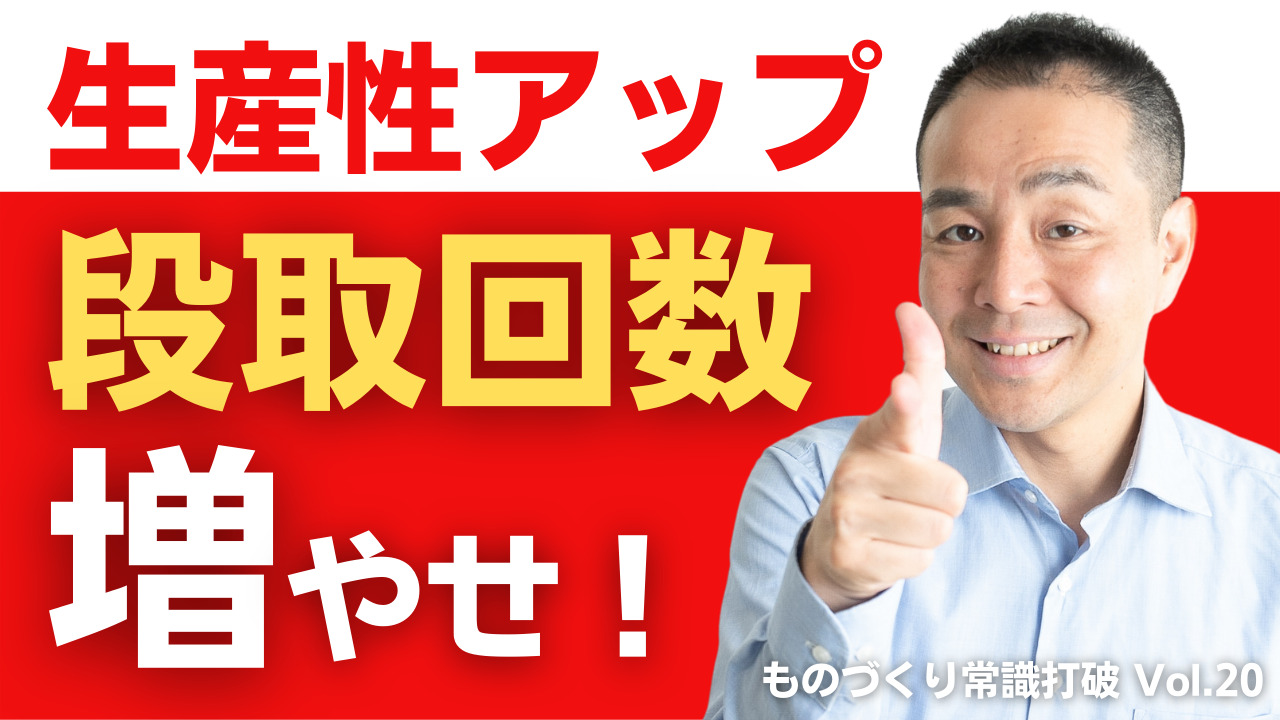
🎯 テーマの概要
- 「段取り時間を減らす」ではなく「段取り回数を増やす」ことが生産性向上に繋がると解説
❌ 誤った常識:段取り回数を減らす工夫
- 一度の段取りで複数ロットを生産する(ロット合併)は納期遅れの原因に
- 必要なものだけをその都度作る「本来のものづくり」を崩している
- 納期遅れはクレーム以上に信頼を失う要因になる
💡 正しい考え方:段取り時間を短縮せよ
- 段取り回数を増やしつつ、1回あたりの段取り時間を短縮
- トヨタ用語:「段取りに始まり段取りに終わる」
- 段取り時間は利益を生まないので最小化すべき
📊 段取り時間のインパクト
- 全作業時間の約3割が段取り
- その半分を削減できれば、生産性は約15%向上
🛠 具体的な短縮手法:外段取りと内段取りの区別
- 外段取り:機械を止めずに準備 → 15~20%削減
- 内段取り:機械を止めて行う作業 → 工夫で外段取り化可能
⏱ シングル段取りの目標
- 段取りを10分以内に抑える「シングル段取り」を目指す
- 一番時間を要するのは「調整作業」→ ここを短縮するのが鍵
📉 段取り時間短縮の3大ポイント
- 金型をあらかじめ機械横に配置(外段取り)
- 金型の調整を不要にする工夫
- 工具類はすぐ使えるようバンドで整理
⏱️ 測定のすすめ
- ストップウォッチで段取り時間を測定するだけで20~30%削減可能
📢 今こそ常識を疑え
- 多くの中小製造業が「非効率な正しさ」に縛られて赤字
- 今こそ、ものづくりの常識を疑い、改革に踏み出すべき
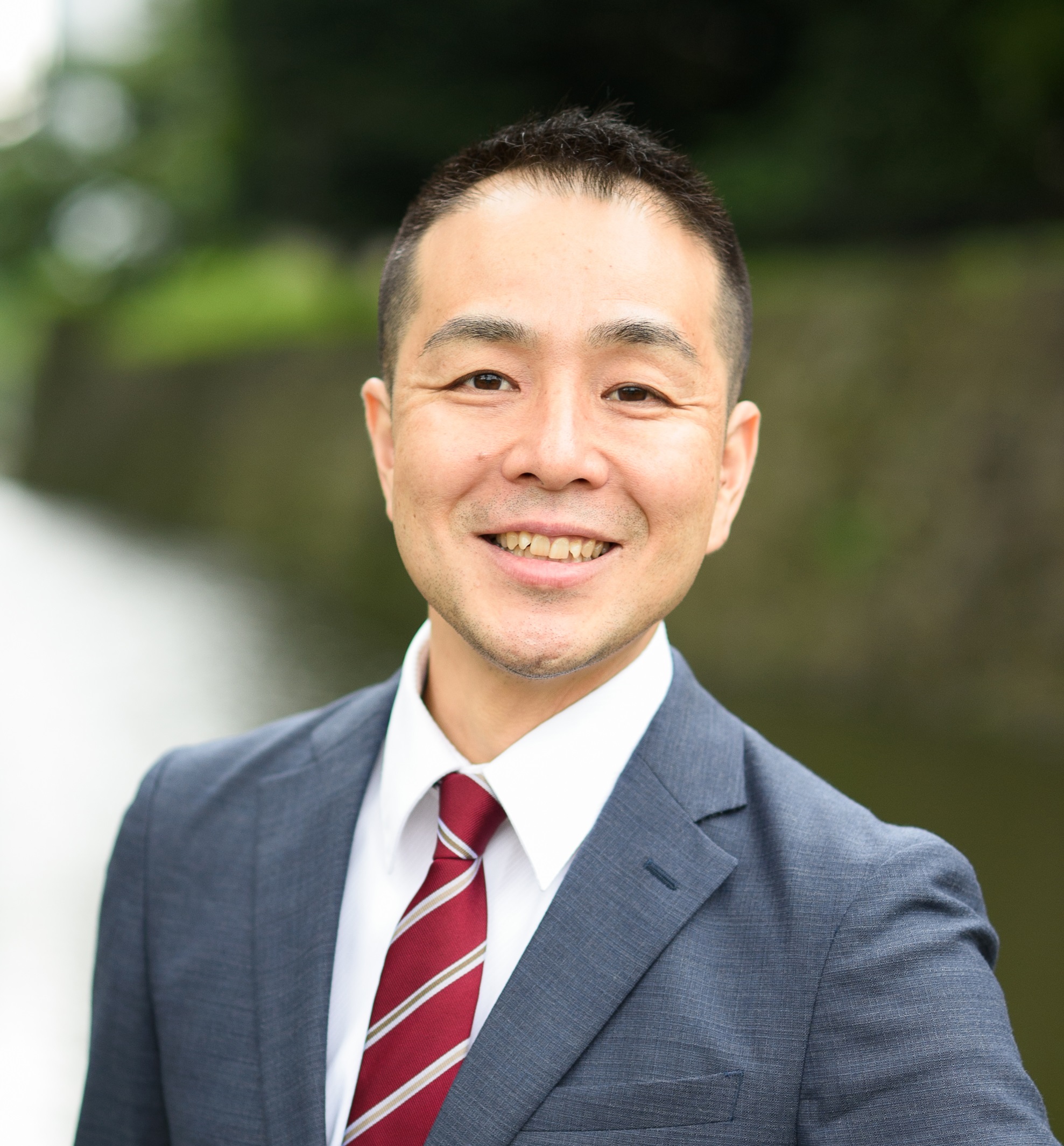
多くの中小製造業の現場では、段取時間を短縮するのではなく、段取回数を減らす工夫ばかりしています
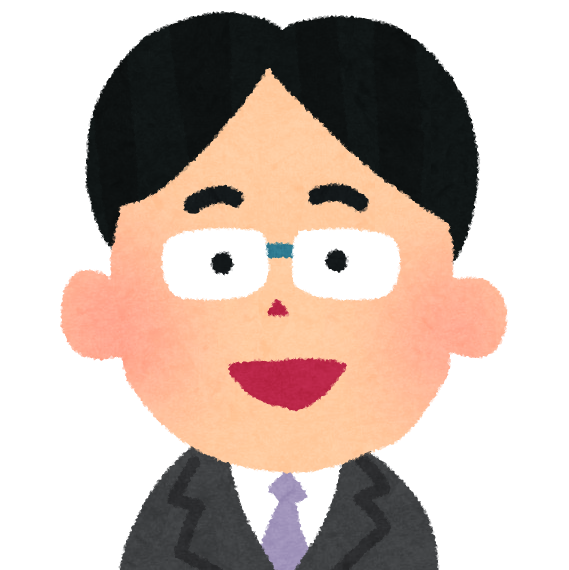
うちの工場では、一度段取したらこの段取で、出来る製品をまとめてつくってしまいますよ!その方が段取回数が減って効率いいですからね
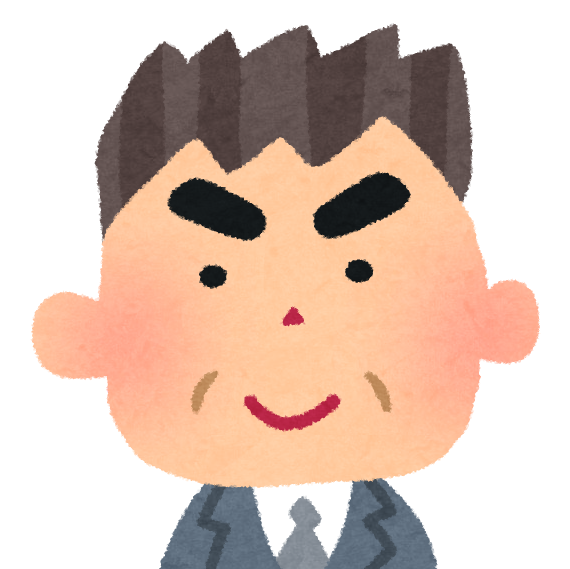
そうだね!うちの工場も同じだよ
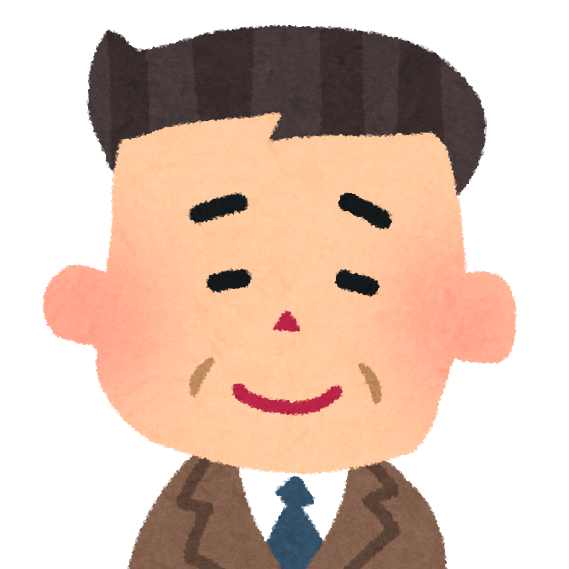
しかし、今回の話では、段取回数を増やせと言っていますよね!・・・うちの工場では、段取回数減らすことで、デメリットが出始めているんですよ
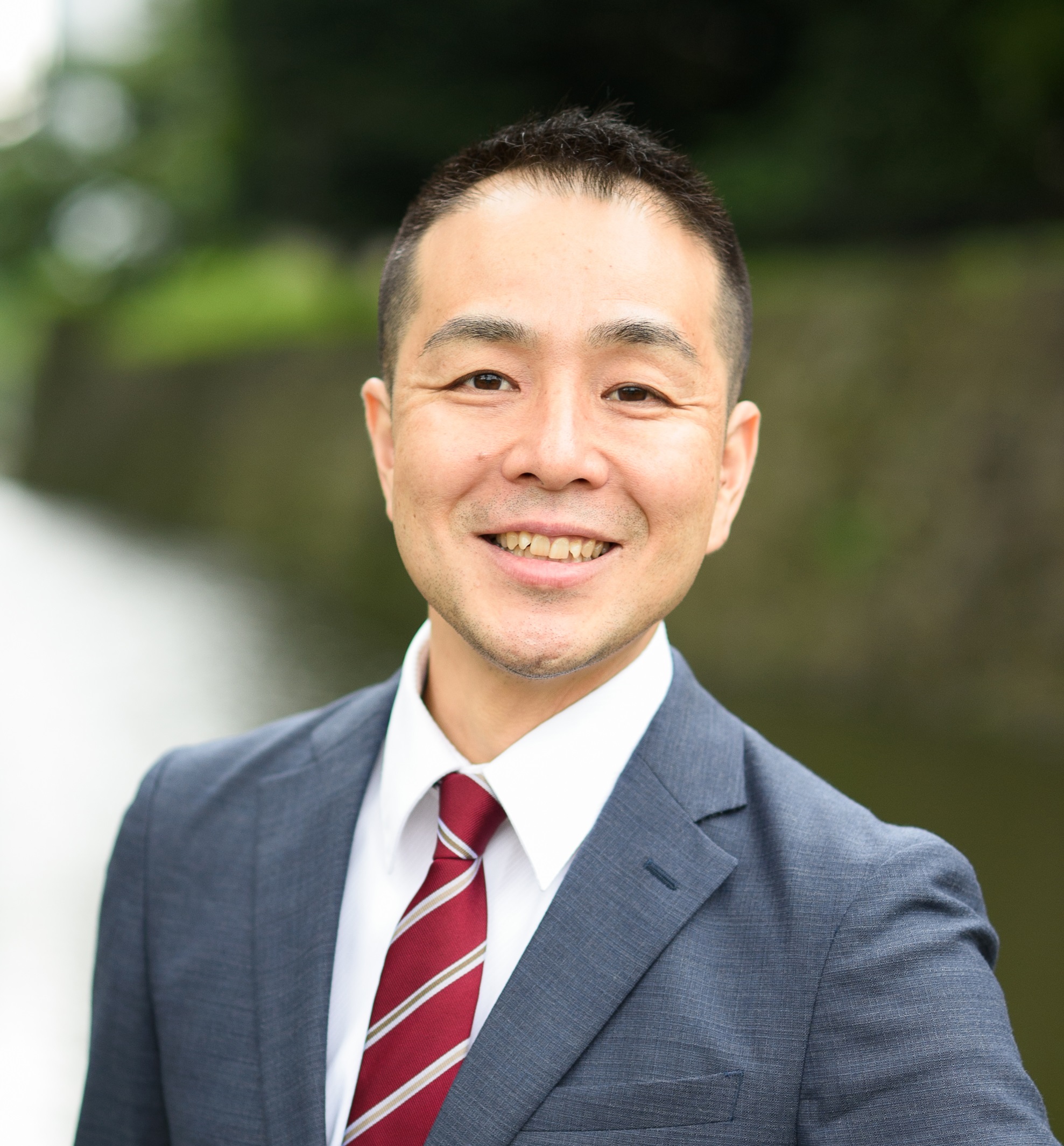
おや、何か気づかれたようですね!実は、この作り方は正しくありません。これをやると本日必要なものだけを作るという、ものづくりの基本を崩してしまうんです
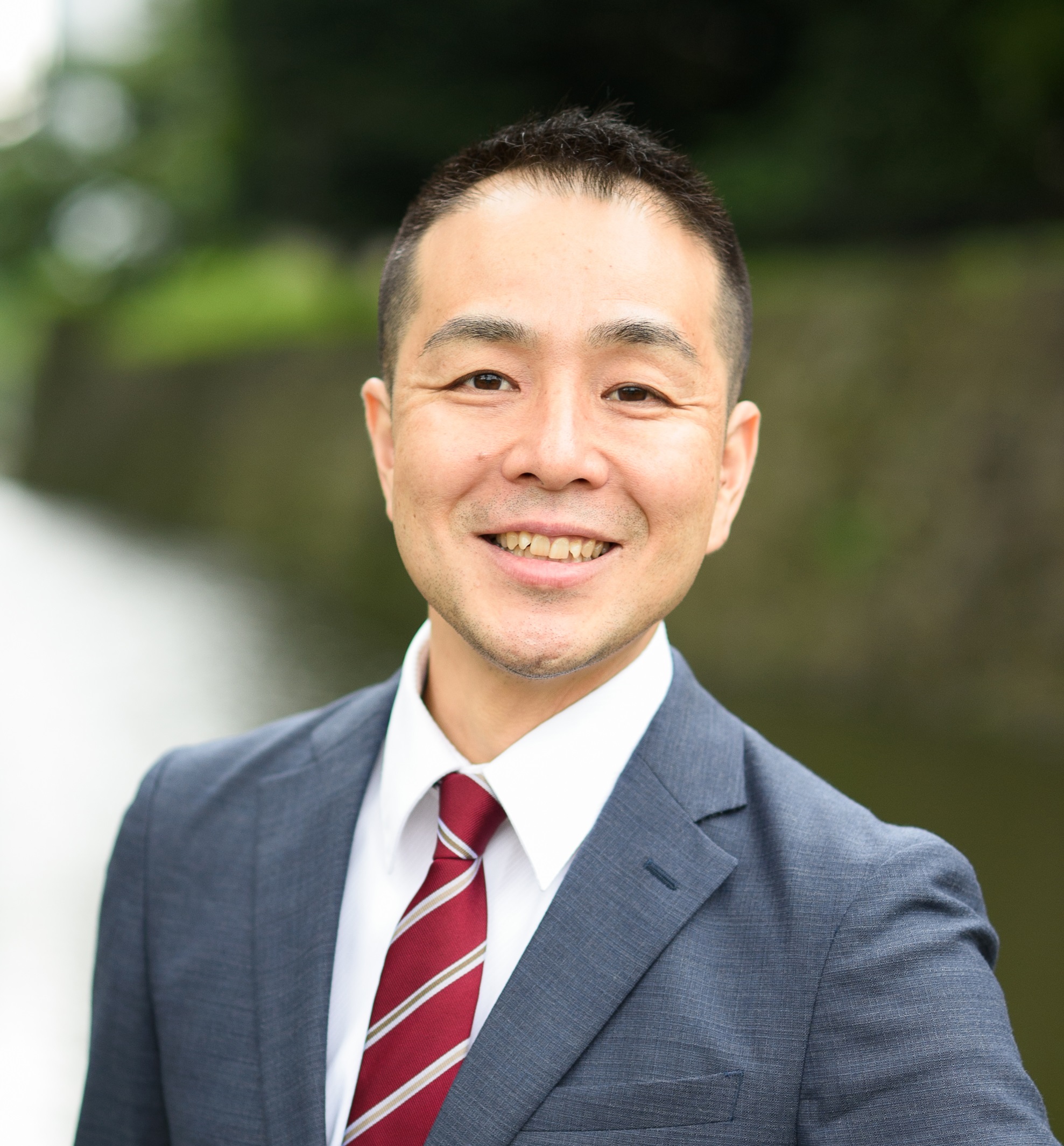
一見効率的に見えますが、これをやると、納期遅れを出してしまうんです!
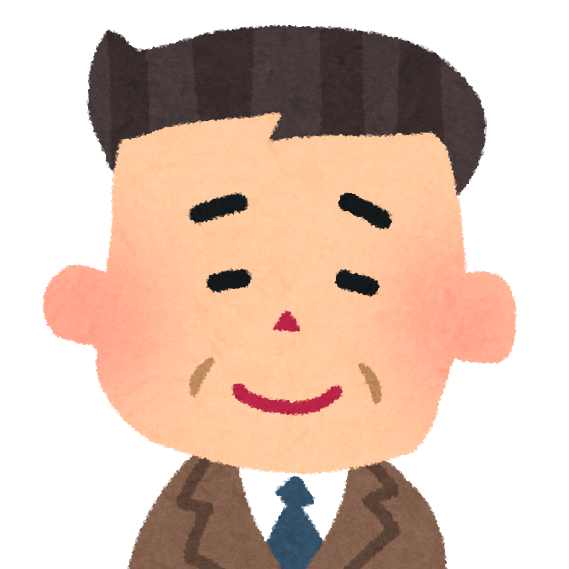
そうなんですよ!ひょっとして、納期順に作るのではなく先の納期品をこの段取で作っているからじゃないですか?!
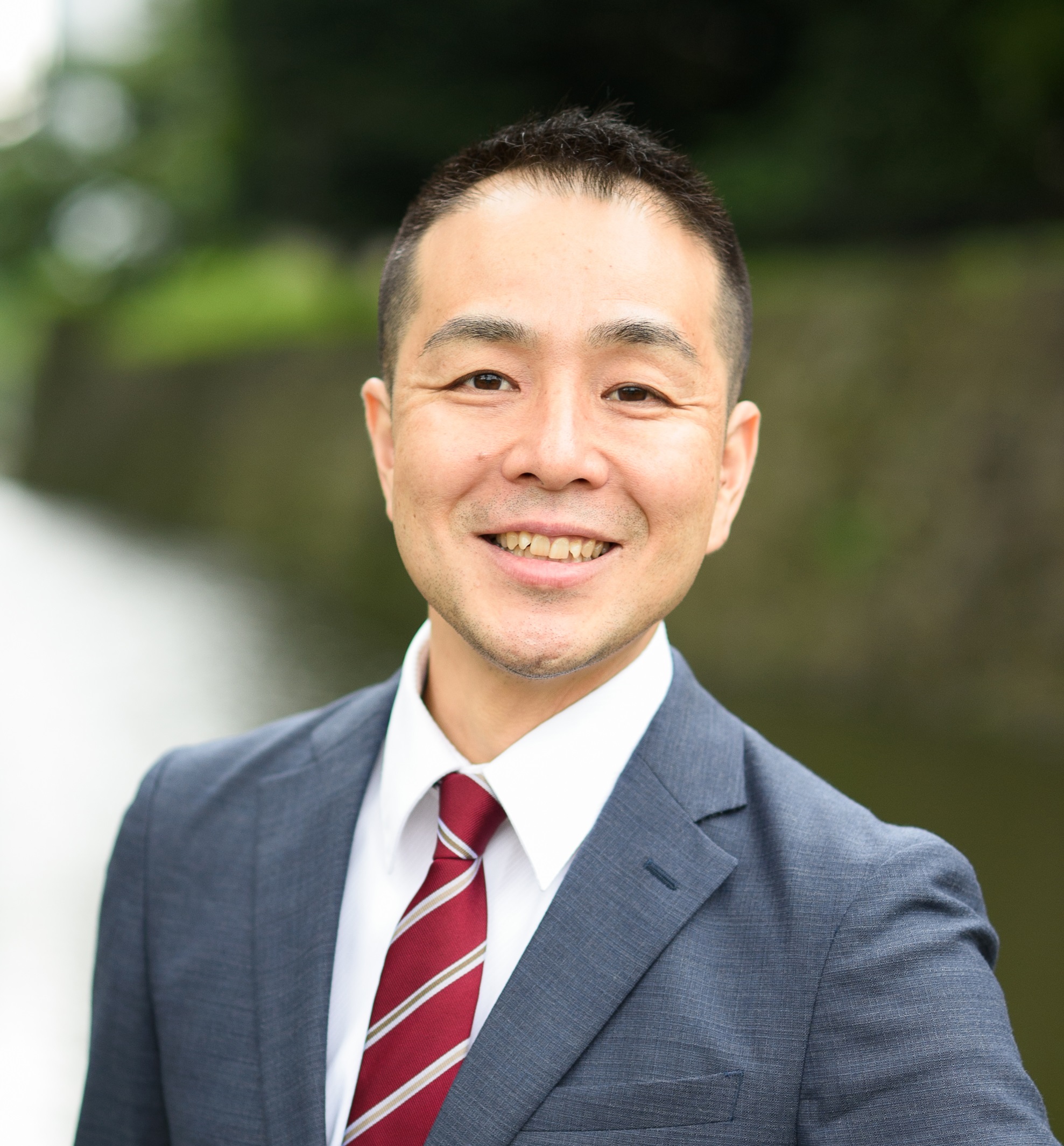
その通りです!素晴らしい気づきです!
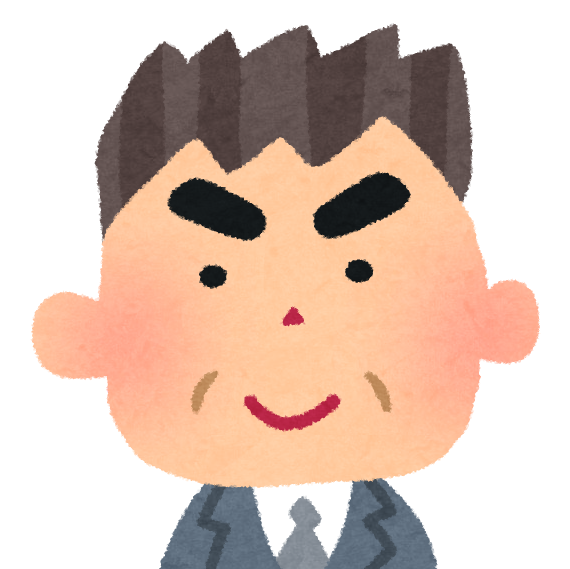
うちでは、納期遅れが当たり前になっているよ・・・
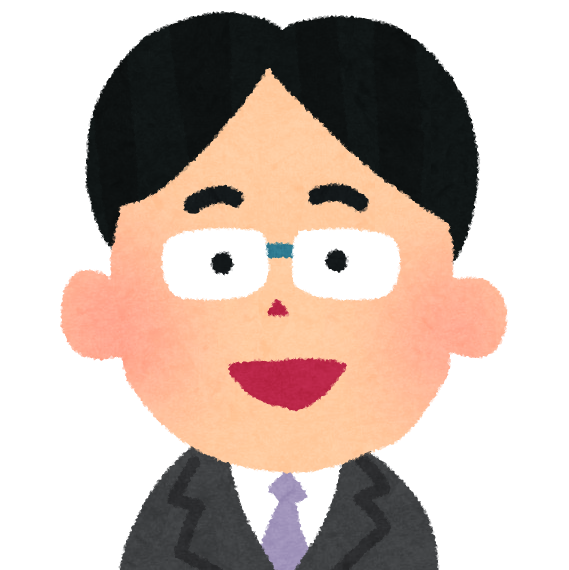
うちもだ・・・
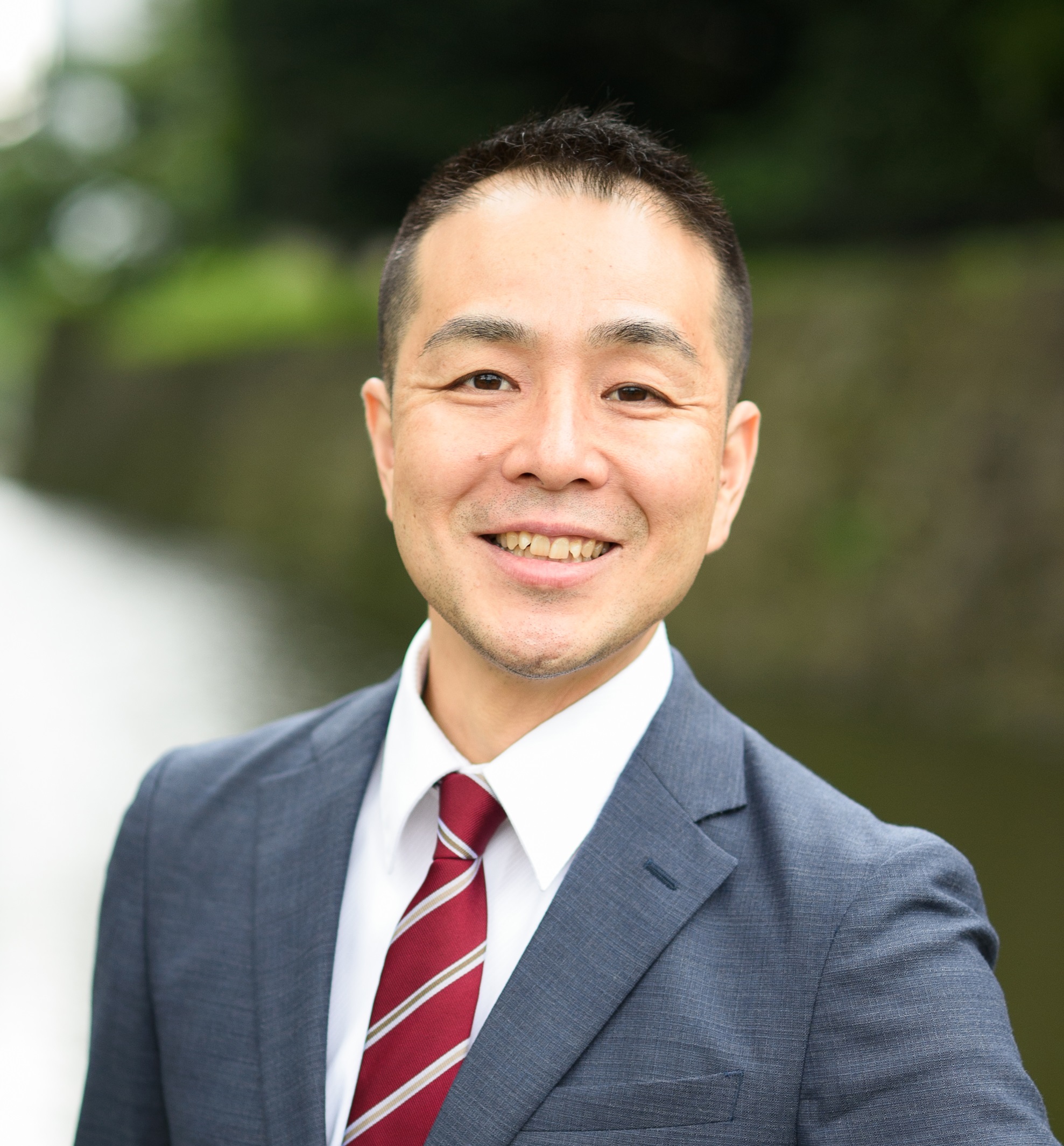
それはいけませんね!今回の話をしっかり聞いてくださいね。必ず解決できますから!
生産管理|生産性向上 段取回数をどんどん増やせ
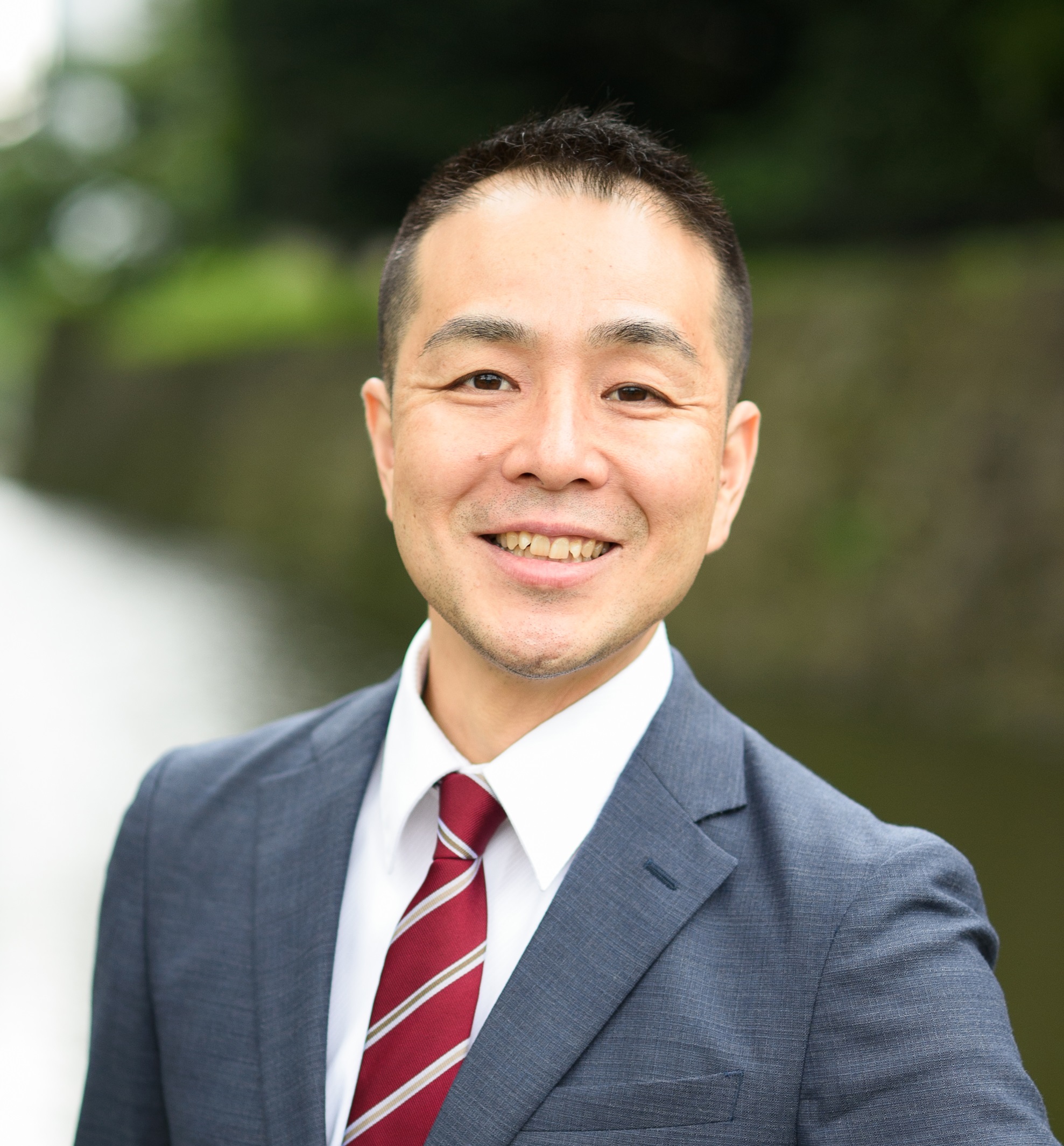
さて、今回の話を聞くことで、段取回数を増やすことの価値、
お金をかけずに直ぐできる、具体的な段取時間短縮方法を紹介します!
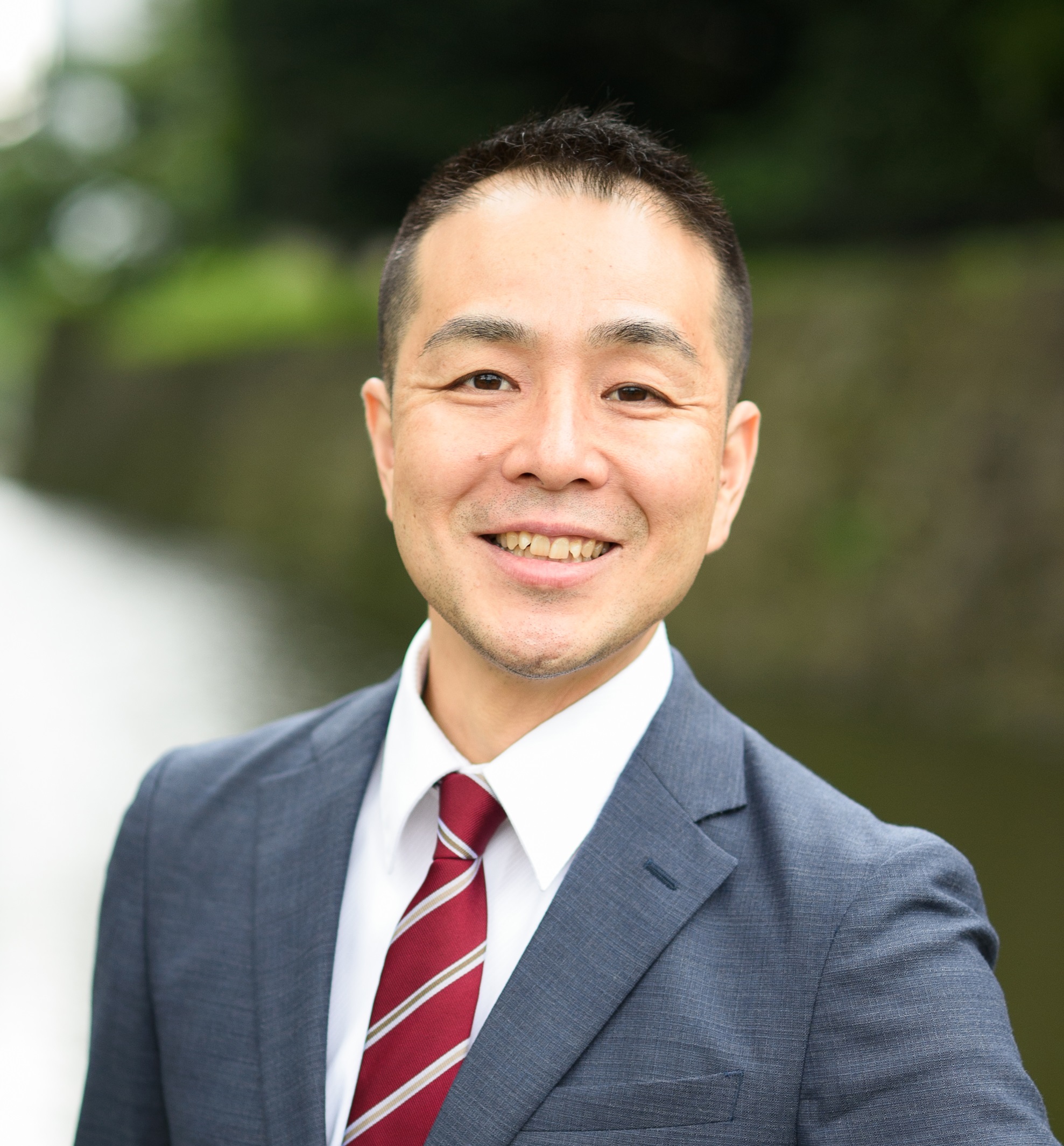
なぜ、段取回数を減らすことがよくないのか?それは納期遅れを出してしまうからなんです。ものづくりにおいて、納期遅れは時にはクレームより罪なんです
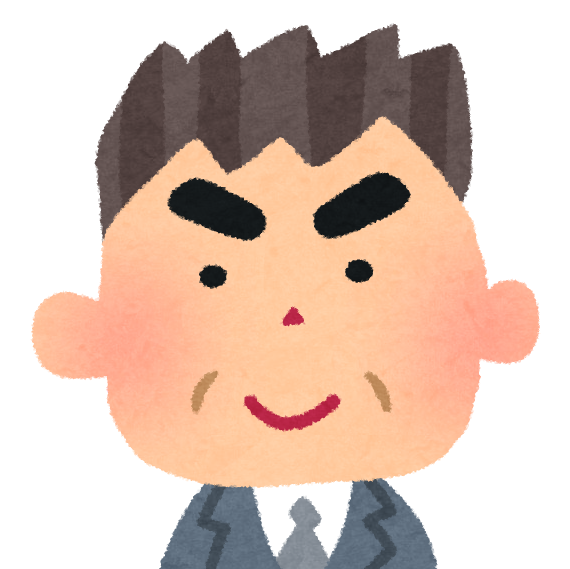
そうなんですね、考えたこともなかったです。
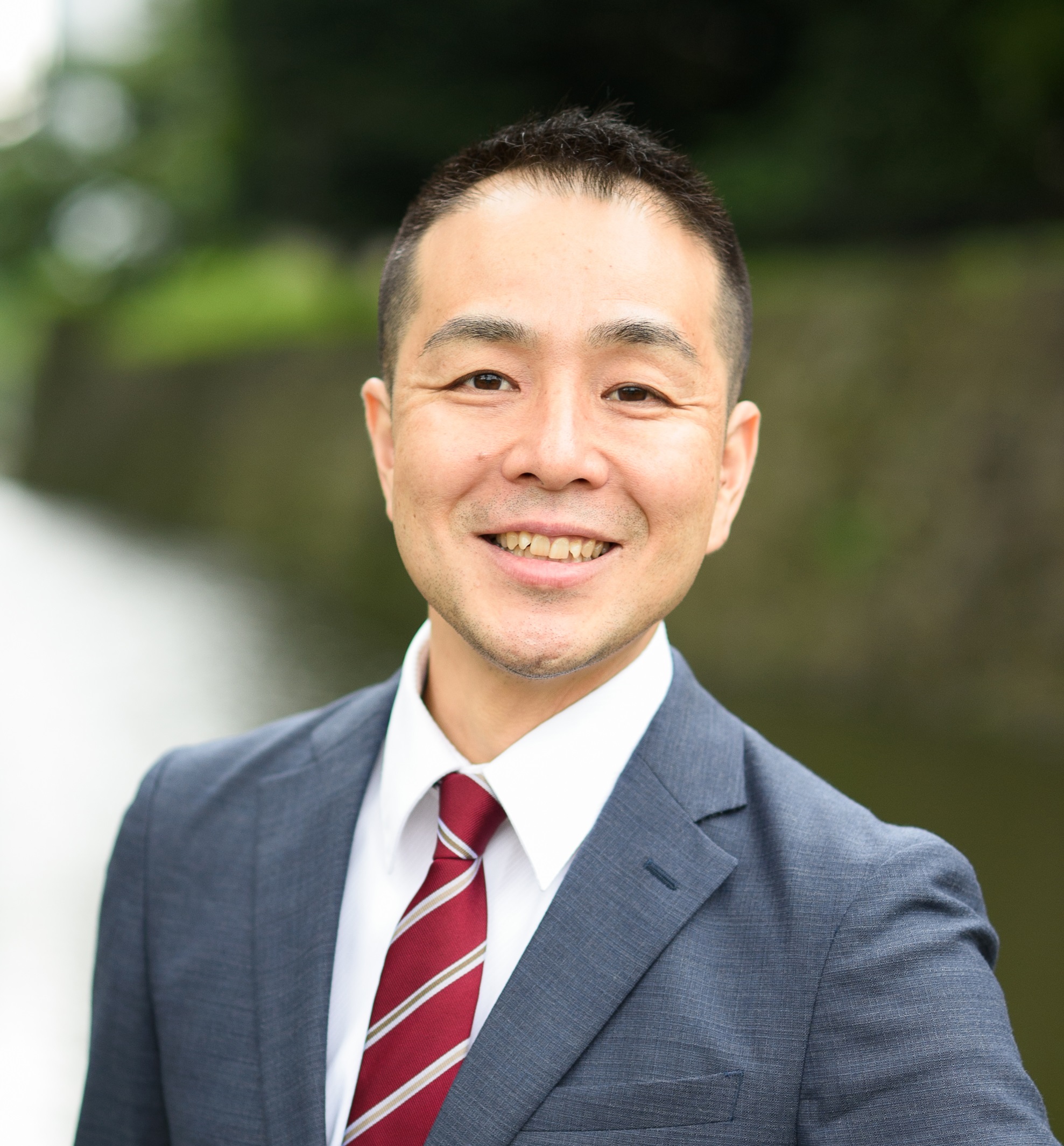
お客さんはさらに次のお客さんを持っている場合がほとんどです。約束を守れない(納期遅延)はお客さんだけでなく、その先のお客さんにも迷惑をかけてしまうんです
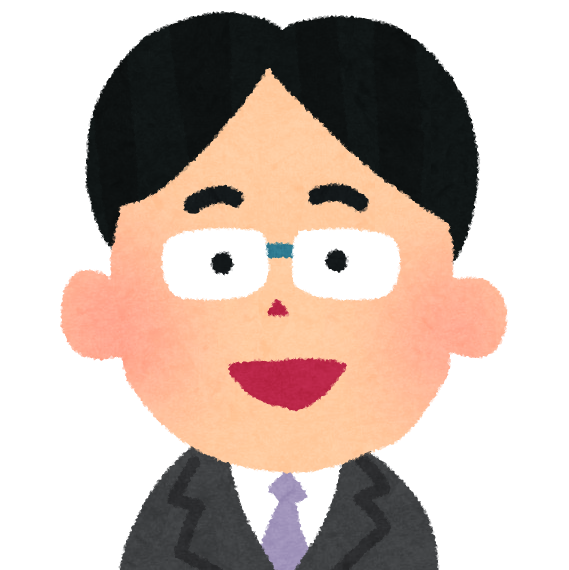
そうですね、納期遅れを起こさないようにします。続きを教えてください。
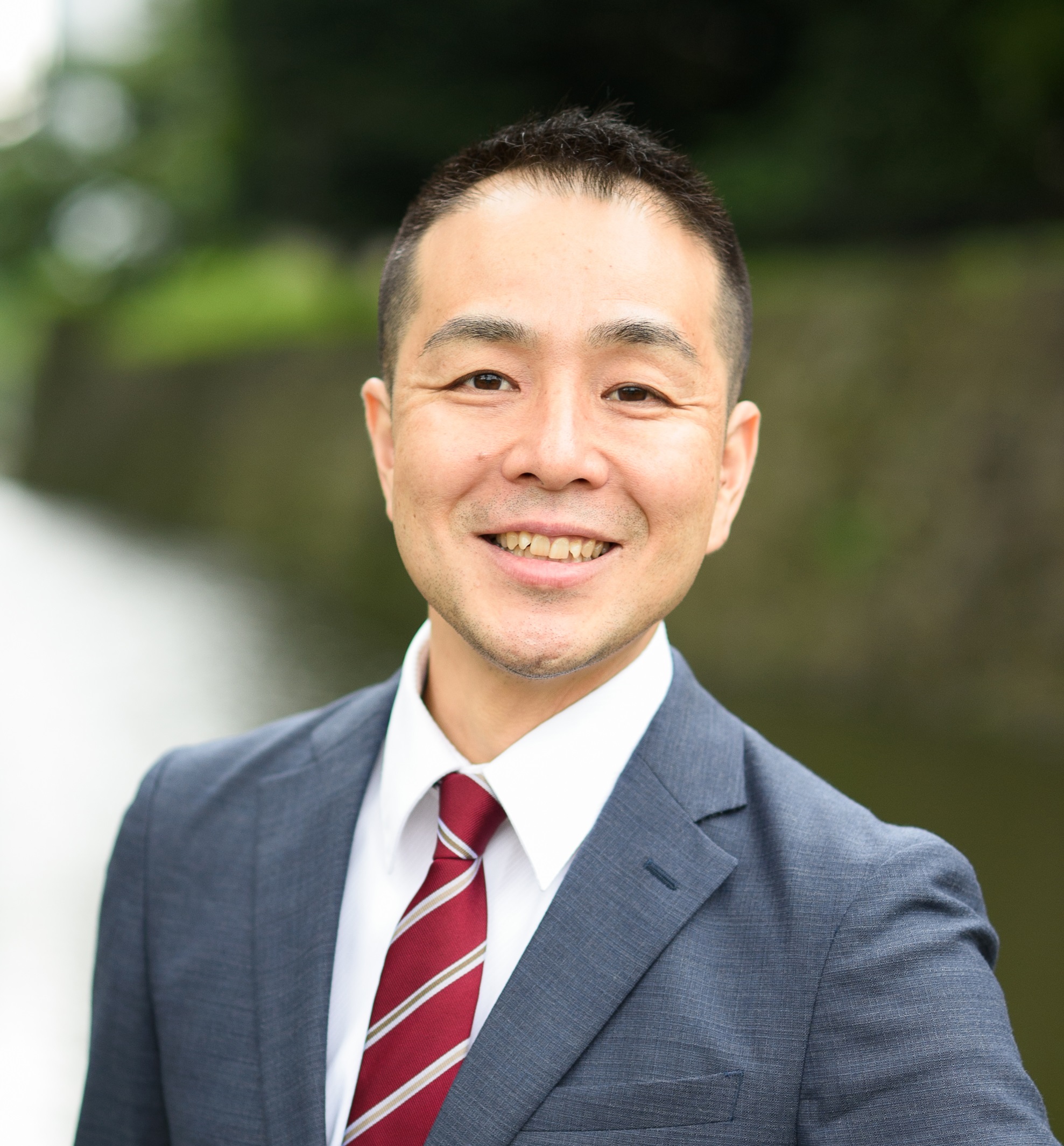
段取回数を減らす例として『ロット合併』があります
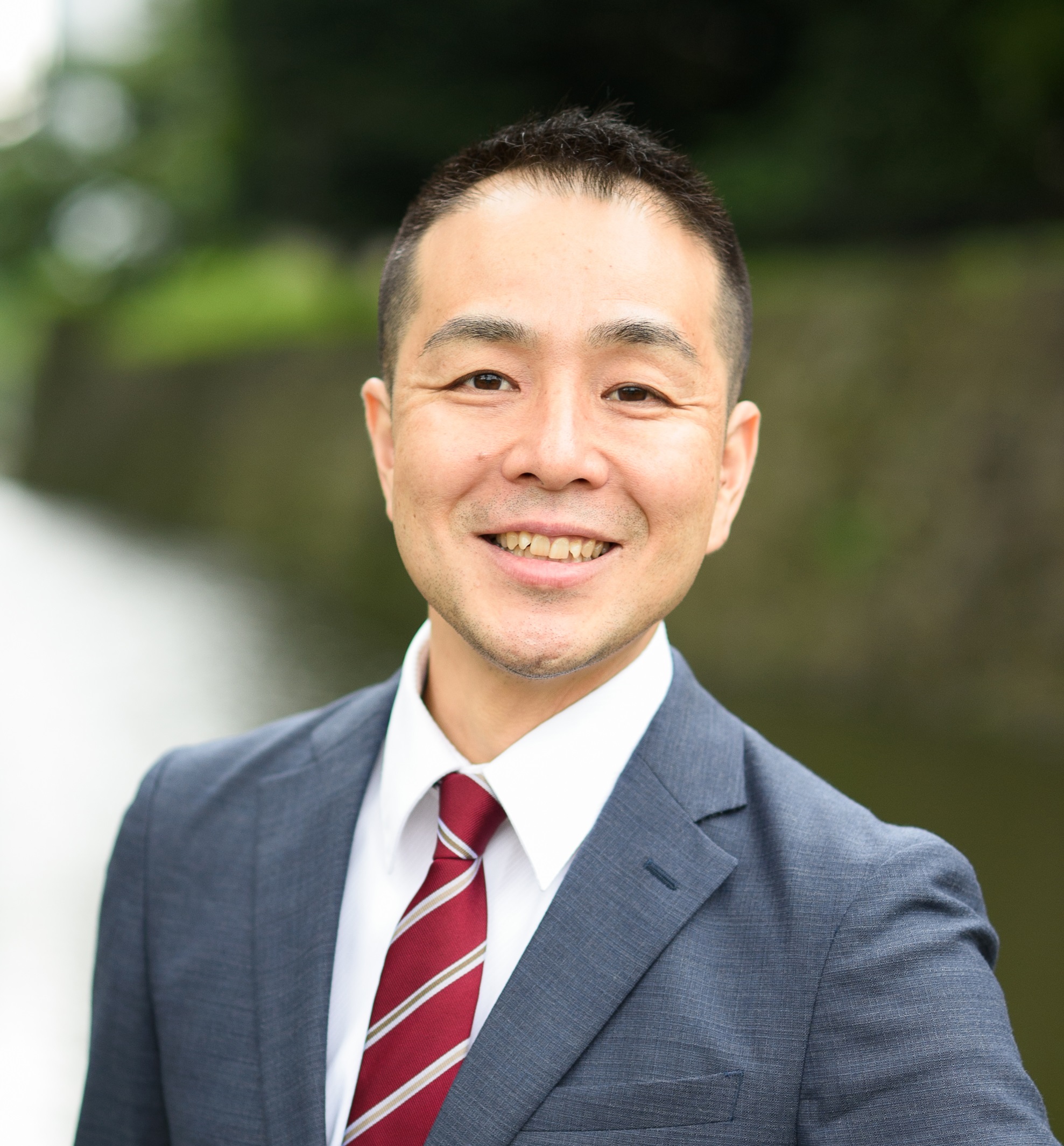
例えば、今週A品を顧客Cへ100個出荷し、翌週に顧客DへA品を100個出荷するとします。このとき、段取回数を1回で済ませることが知恵と考えて、200個をまとめて作ってしまうんです
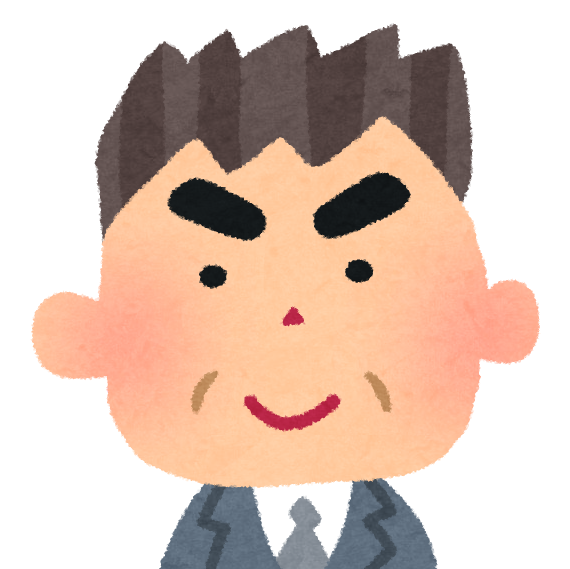
ロット合併ですか!正にうちがやっていることです
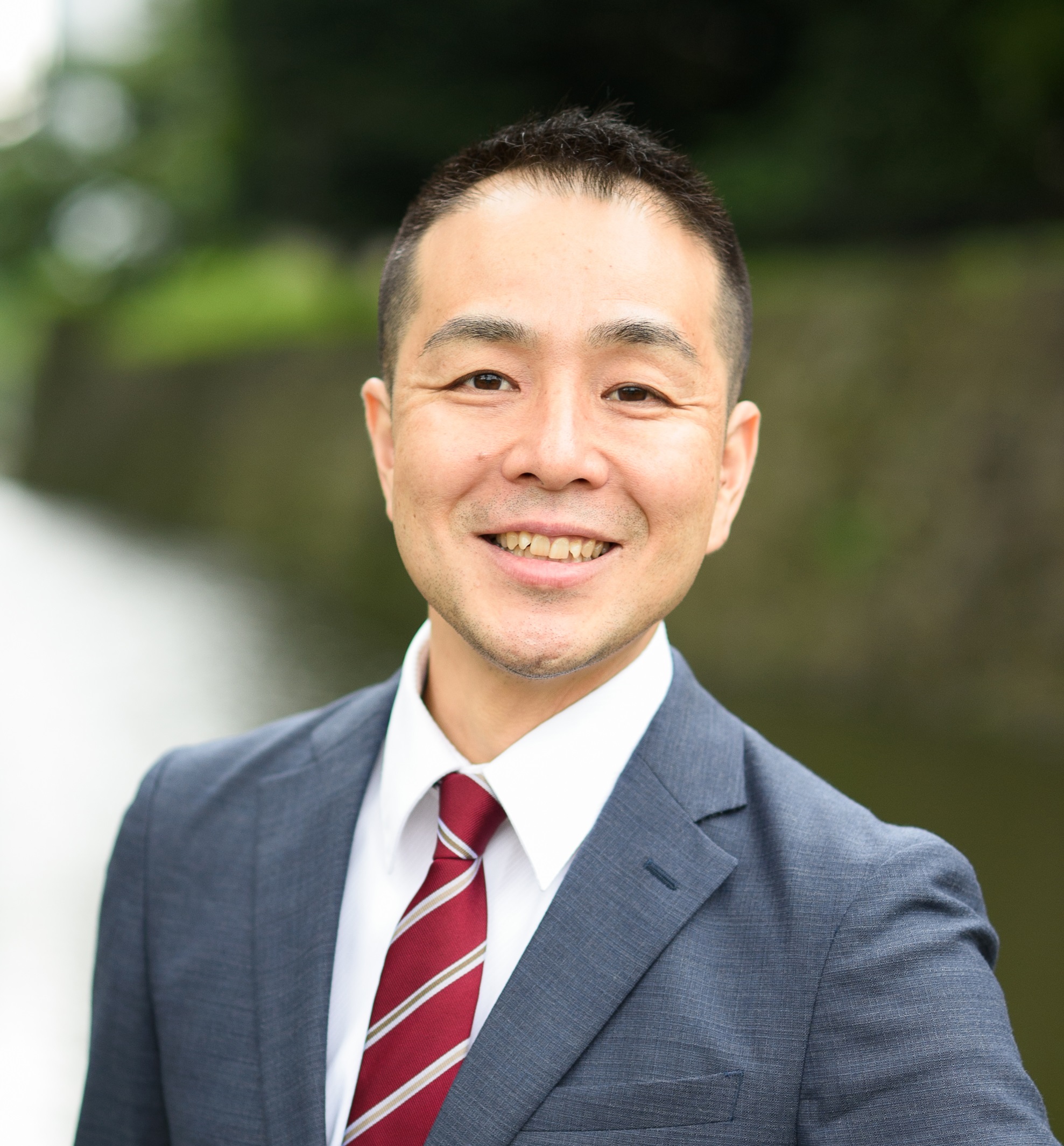
1製品だけでなく複数製品をロット合併するため、今週作るべき出荷製品が生産に入らなくなってしまうんです
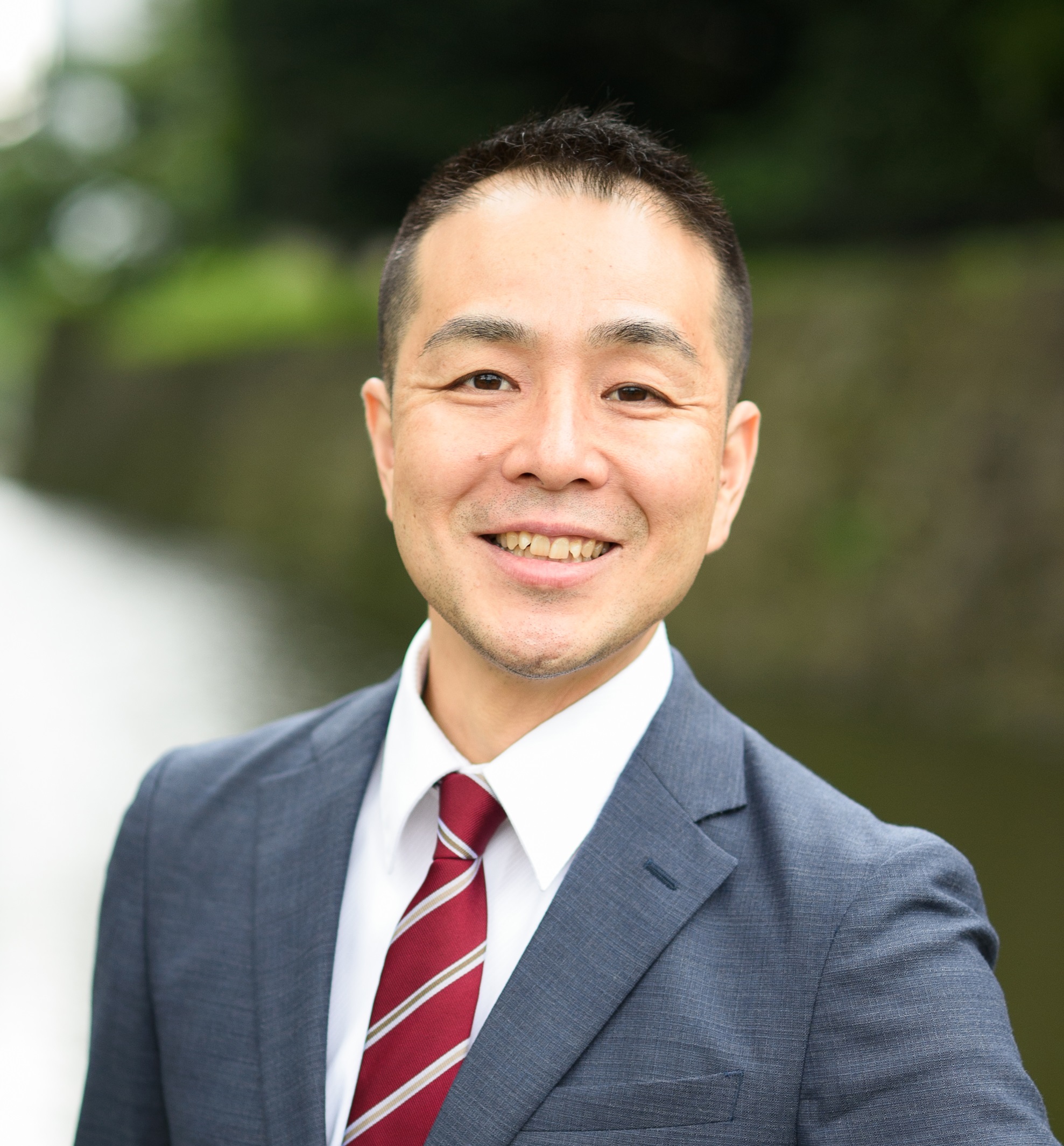
そして、納期遅延という副作用をだしてしまうんです。実は、この副作用である納期遅延に気づかないことが問題なんです!
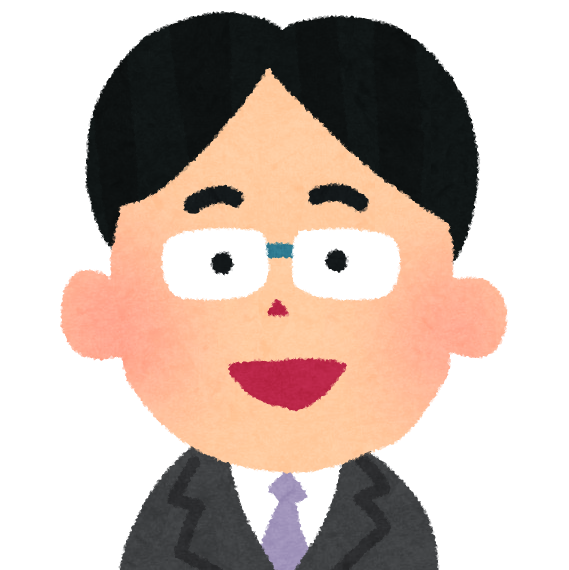
なるほど、やっと理解できました。
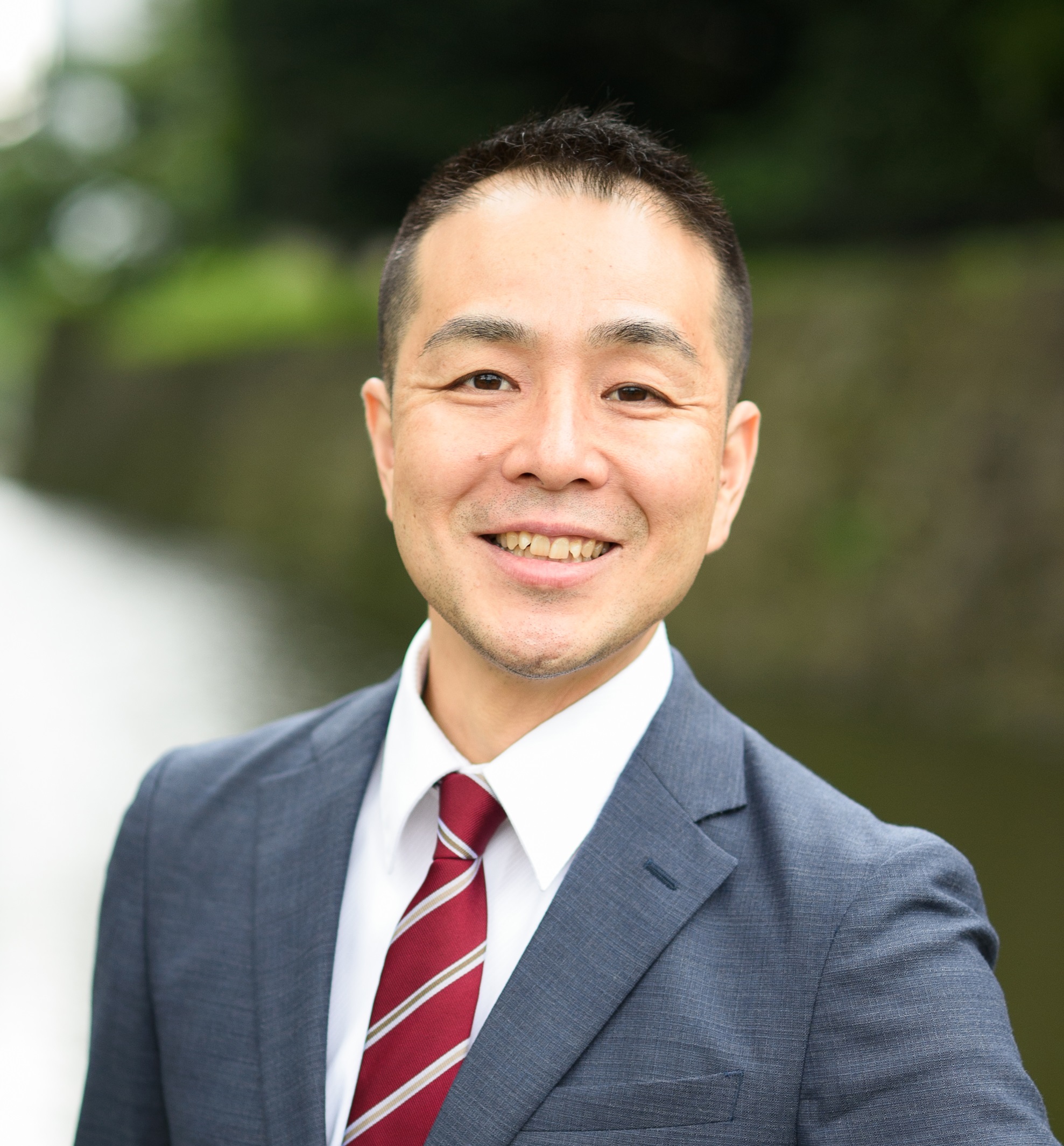
この問題の発生根拠は、1回当たりの段取時間を短縮改善するのではなく、段取回数を減らすことが「知恵」だと考えていることにあるんです
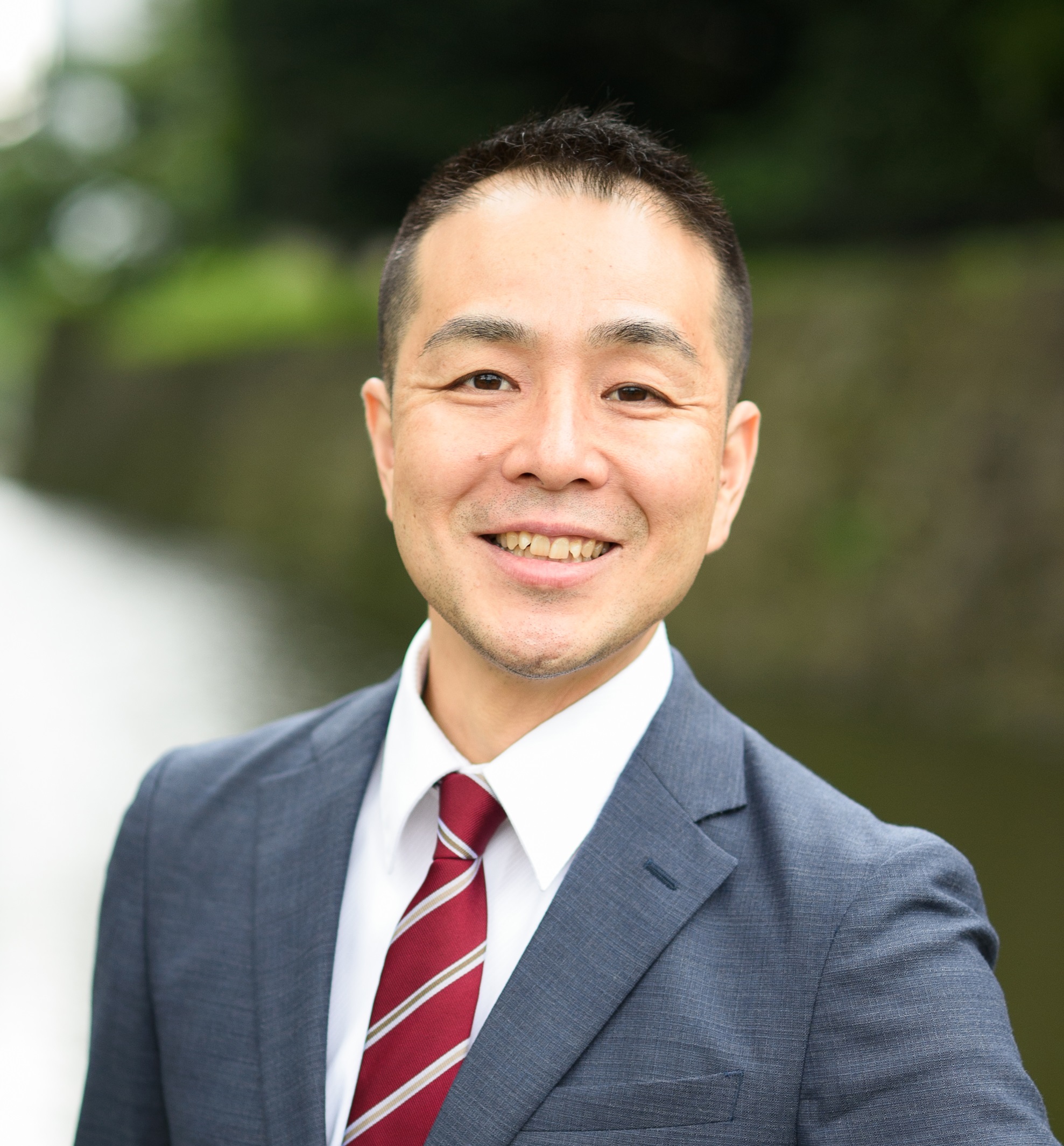
これがものづくりの盲点であり錯覚なんです!
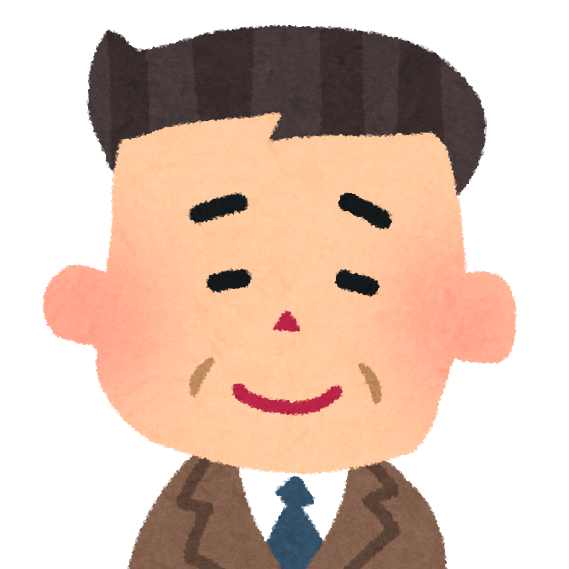
では、どうするか?続きは動画で詳細を確認ですね!
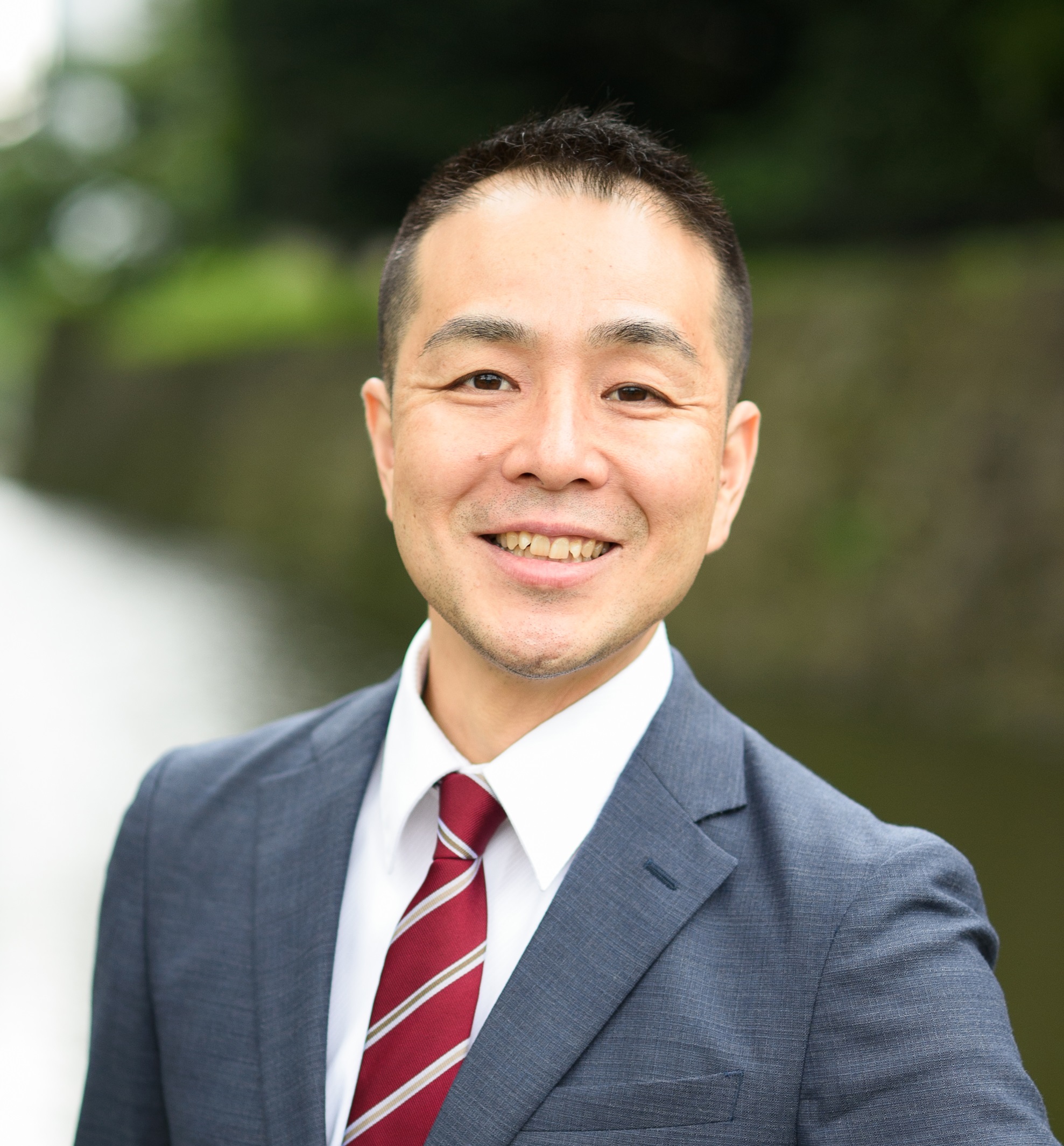
はい、その通りです。ご質問があればいつでも聞いてくださいね
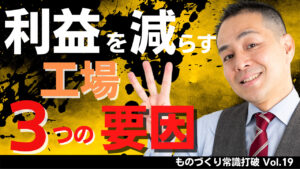