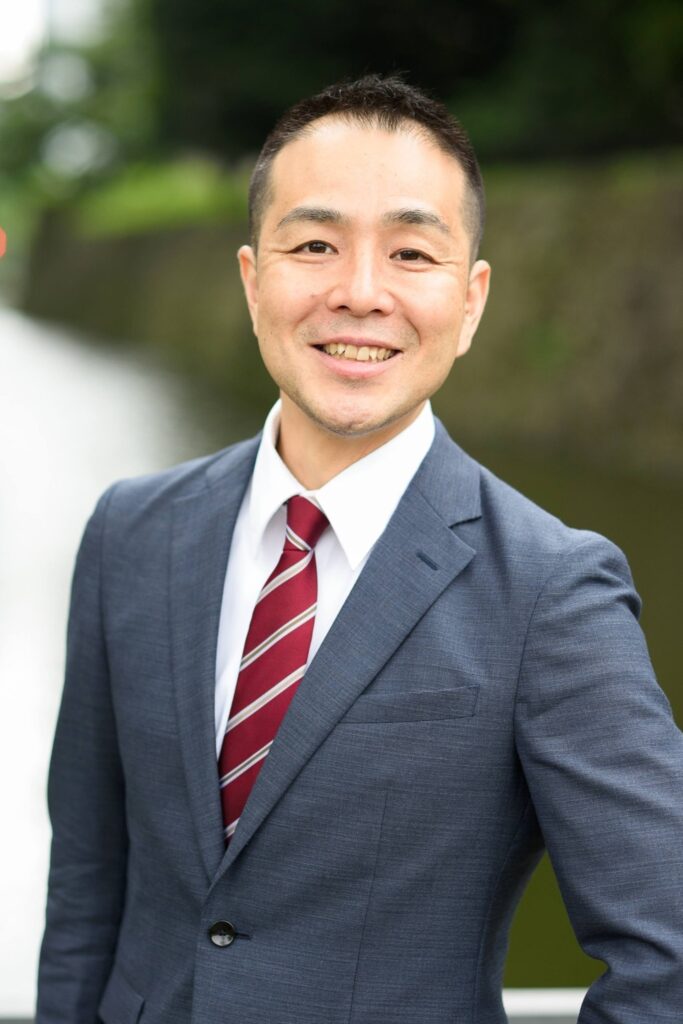
糟谷 徹(カスヤ トオル)
合同会社Betters代表経営責任者
カスヤ技術士事務所 代表
元 近江技術士事務所副 所長
週休2日で利益率300%を約束できる工場学
「ほったらかし経営」開発者。
大手製造業と中小製造業の
現場を研究開発から工程設計、
海外工場の立ち上げから、
品質管理までを実務で20年間経験。
ISO9001主任審査員
ISO9001認証取得員として
認証取得指導35社、
398回(617日)の審査実績を持つ
近江堅一氏より継承した、
29年間で490工場以上を黒字化に導いた
日本で唯一の、
生産性向上プログラム「FL法」を
『工場学』という形で
令和版にアップデートし、
令和7年まで
46社(10業種)の工場の利益率を
向上させることに成功。
金属加工、精密部品加工、
プラスチック成形、縫製業、
食品加工、鍛造業、ゴム製品加工、
電子部品製造、鉄鋼業、印刷業、
コンサルティングを行なうことで
22社が3ヶ月で利益率向上のしくみを完成し
異例の再現性を誇る。
売上貢献額は合計30億円を超え
その実績と確立されたノウハウは
Youtubeでも注目されチャンネル登録者は
6,500人弱に急成長。
著書「中小メーカー向けトヨタ生産方式(FL法)の教科書(セルバ出版)も重版が決定。
他著書、お金をかけずに5か月間で30%生産性を上げる秘訣
一度コンサルティングに入ると
社長が動かなくても
利益が伸び続けることから
巷では
「糟谷再生工場」と言われるほど
講演依頼、コンサルティング依頼が
絶えない逸材として注目されている。
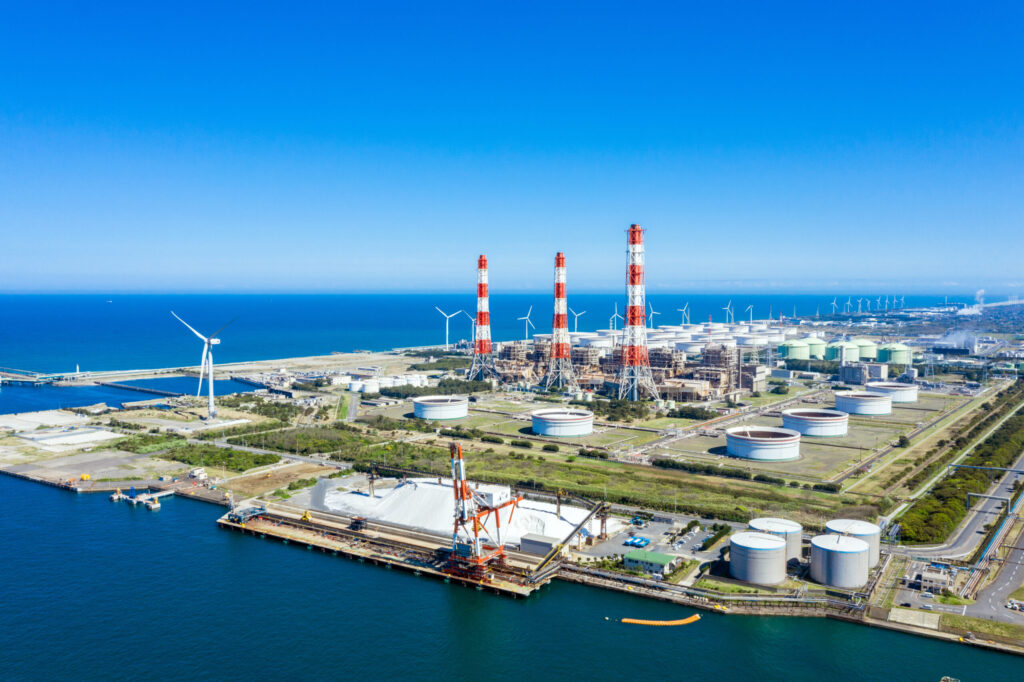
2024 年 3 月現在。日本には約 45 万社のものづくり工場があります。
その中で黒字経営をできている工場は約 55%。
日本経済を支えてきた ものづくり工場が今、厳しい状況になっています。
私自身、17 年 10 カ月(18 年)の工場勤務の中で
現場責任者を務めた経験から「この状況をなんとかしたい」という想いから工場黒字化コンサルティングをスタートしました。
そして今まで弊社は、
43 社(※令和 6 年 12 月時点の実績)の工場のコンサルティングをし
利益率 300% の黒字化経営に導いてきました
といったように。
なぜこのようなことを実現できるのか?
新しい機械や設備、コンピューターシステム等を導入するなどのお金をかけずに(新しい経費をかけずに)
利益を伸ばし続ける方法を知っているからです。
20 数年前、私は大学院修了後、
某メーカーに就職し 8 年目の現場責任者時代、工場改善チームを立ち上げました。
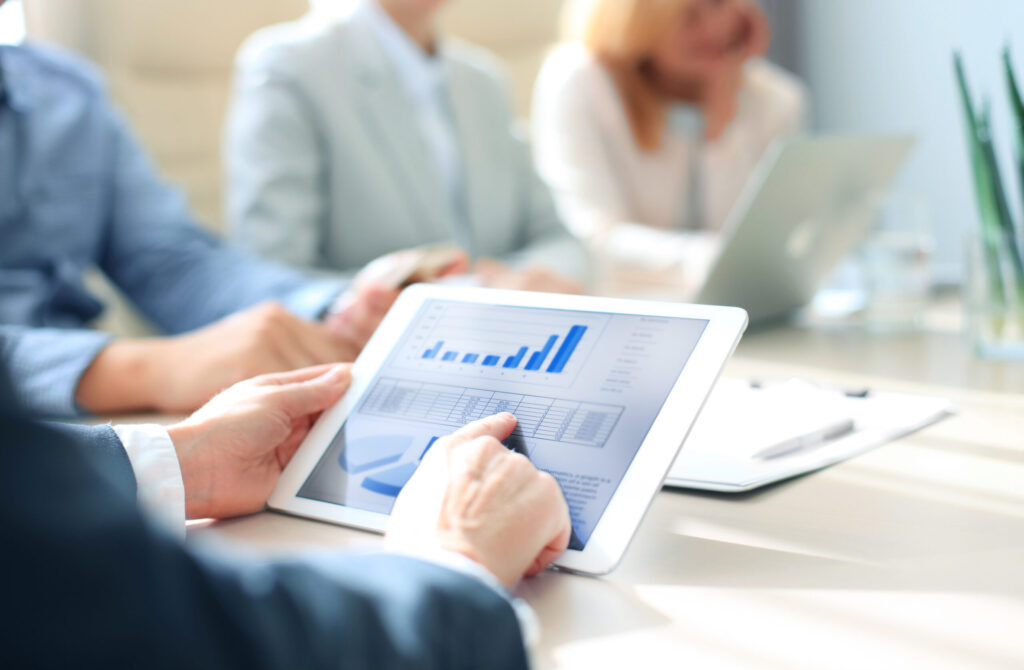
工場で仕事をする中で、仕事は現場任せ、誰も管理していない、というやり方に、違和感を感じたからです。
そして、工場のムダを排除することや、品質問題の解決に取り組みました。
しかし、 当時の私の考え方は甘く
そう簡単に工場の利益を伸ばすことができませんでした。
そのうち、
ウチも沢山のクレームで倒産することになるのか…
私だけではどうすることもできない…
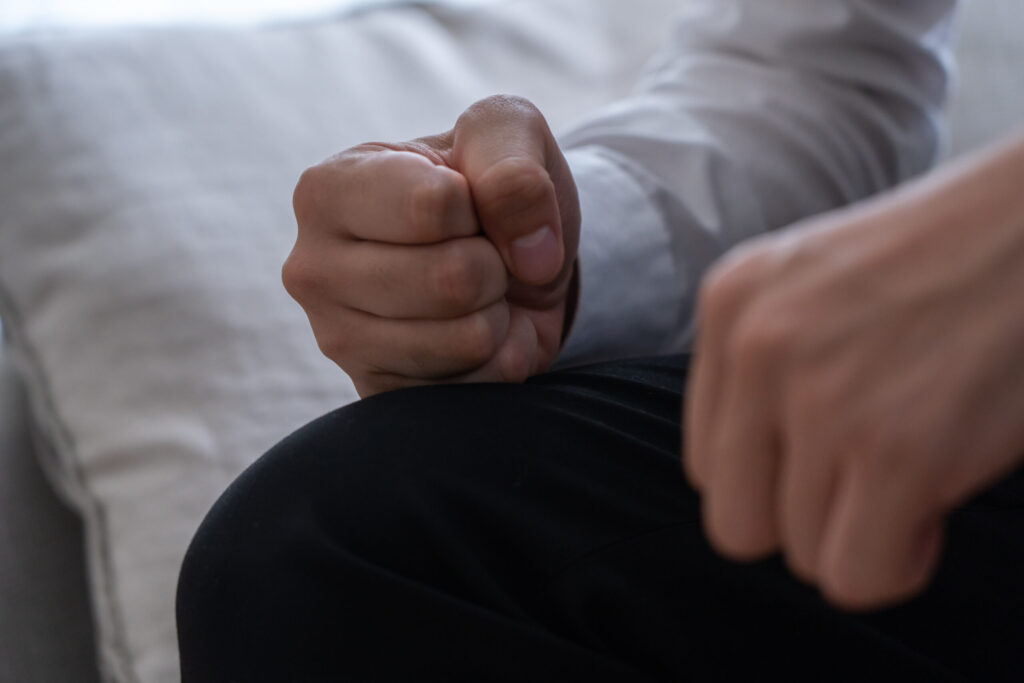
絶望したことを 今でも夢に出てくるくらい悔しかった想いを鮮明に覚えています。
更なる学びをスタート
その後、「なんとか黒字にする」そう奮い立った私は、工場管理や品質管理の実務経験を積みながら、
技術者最高の資格である技術士(経営工学)や品質管理検定 1 級を取得。 更には、トヨタ生産方式を確立した大野耐一先生の愛弟子に指導を志願し、モノづくり哲学の真髄を学んできました。
そして 品質問題、設備トラブル、ムダの排除など、毎月数十万円のコスト削減を実現しました。
「このノウハウを多くの現場責任者に伝えたい!」 そう思った私は、ある技術士の先生に出会いました。近江堅一先生(技術士、経営工学)です。
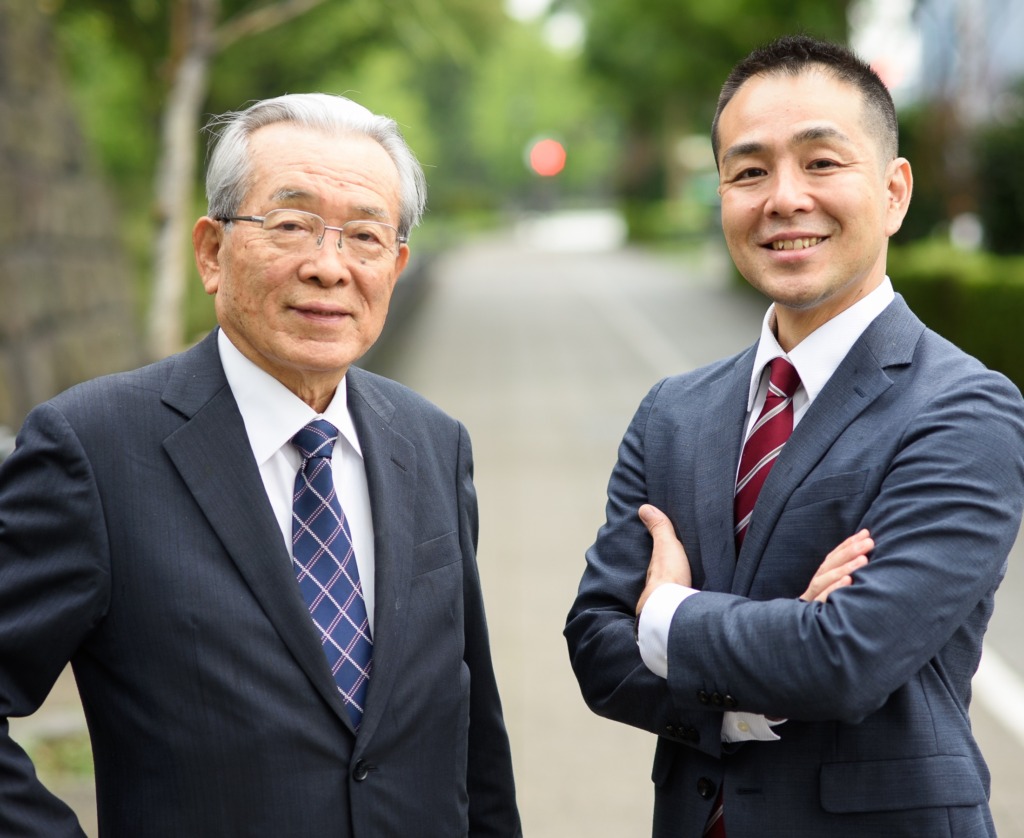
近江氏は、トヨタ生産方式の思想ジャストインタイムを具現化し、お金をかけずに工場の生産性を上げることで
利益を生み出す工場改革手法、
「中小製造業向けトヨタ生産方式」(FL 法)を確立した人物です。
本業の傍ら、毎月の指導に同行させてもらうようになりました。
近江氏が確立した FL 法は、これまで 29 年間、
500 社以上に導入され利益率が 300%以上になった実績があります。
そして、今私は近江氏のノウハウを受け継ぎ、更に方法論だけではなく、
クライアントの行動変容を最優先にすべく、行動経済学や脳科学の方法論を体系化して
『工場学』としてアップデート、進化させながら、コンサルティングを行なっています。
工場学をやるとどうなるのか?
今、工場管理者に必要な「教育」とは、技術力の向上や品質の確保ではありません。
『今の仕事のやり方を、いったん白紙にして、ゼロから再構築していく』ということです。
そして、この挑戦を管理者自身に体験してもらうことが、管理者教育の本質です。
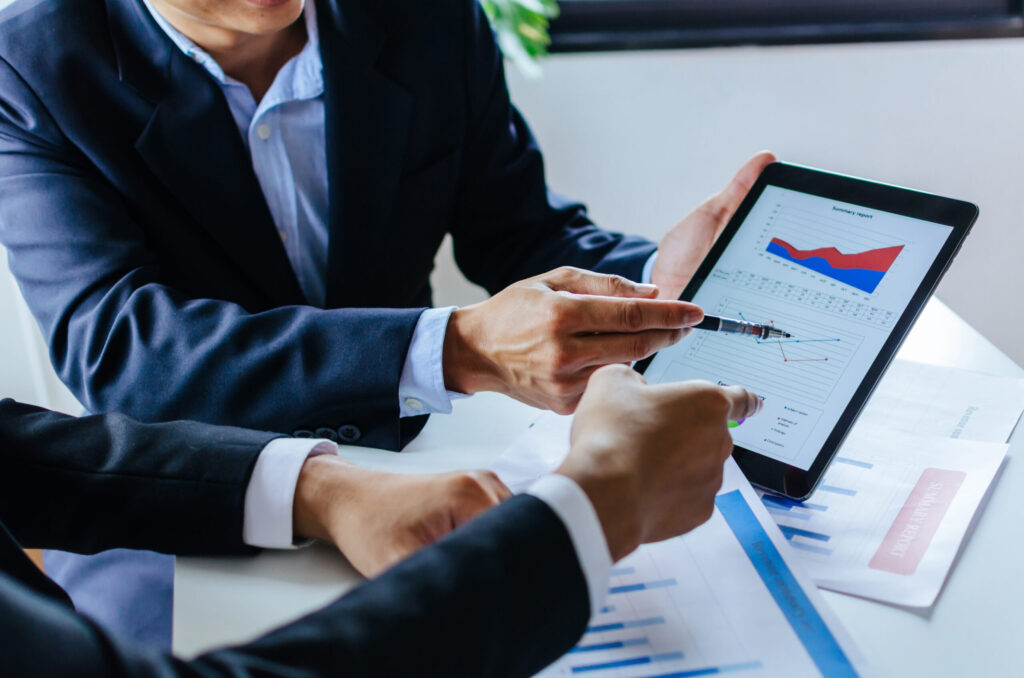
利益を最大化する仕事のやり方を、管理者自身が新たに構築していくという過程で、
生産性が向上し、利益率 300%を実現できるのです。そして、管理者は成長していきます。
また、工場学の最大の特徴は、『おばけ退治』です。
殆どの中小メーカーは『時間指示』の生産計画を出していません。
『時間指示』がないと、作業者は勝手にトイレに行ったり、
休憩したりして『お金を生まない時間』が増えてしまうのです。
この『お金を生まない時間』をおばけと呼びます。
おばけを退治するには『時間を入れた作業指示』をすることです。だから、おばけを退治すれば生産性が一気に上がるのです。
私が、あなたに一番お伝えしたいことは、
『工場にはまだまだ改善できることが沢山ある』ということです。
ただそれが『見えていない』だけなのです。
そして『見えていないものに気づく』ことです。
『気づく』ことにかかるお金はゼロ円でしかも時間は殆どかかりません。だから、1 社でも多くの工場に気づいてほしい、というのが私の願いです。
私は、
もっと沢山の工場の力になりたい!もっと工場学を伝えたい!それにより、日本中、全ての工場に関わる人達が幸せになる!
日本のものづくりはもっと伸びていき、日本経済を支える工場が増えてくる!中小製造業が日本経済を救う!
この様な、気づかせる活動を継続していくことが私の使命であると思っています。
サービスの流れ
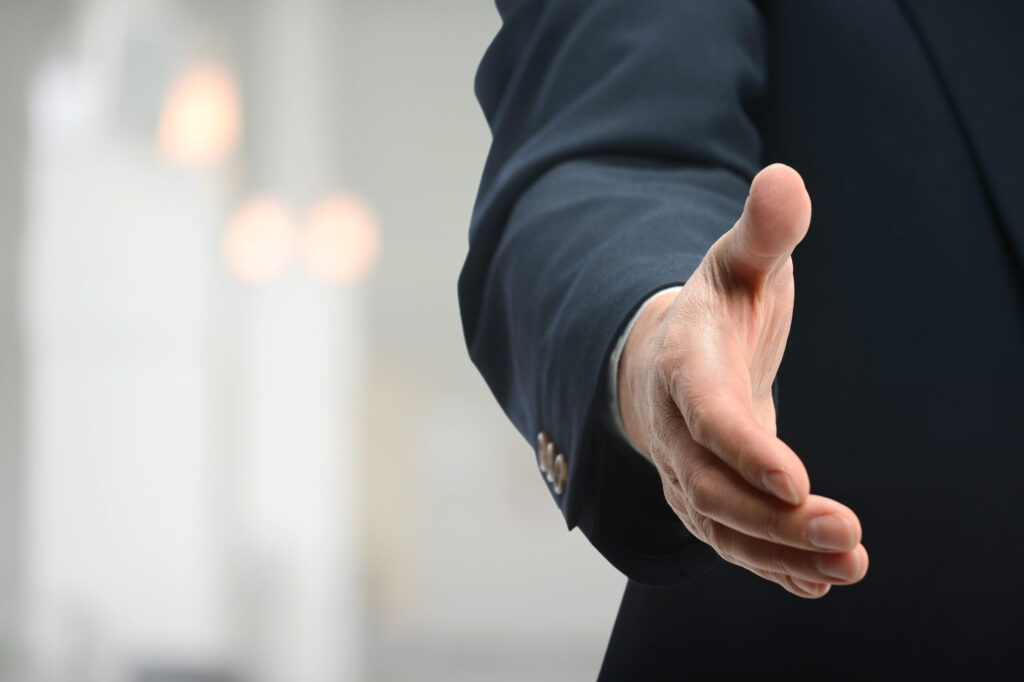
“カスヤ技術士事務所”は、どのような活動をしているのですか?一貫して中小製造業の生産性向上を支援しています。
特定の業種に限定しているわけではなく、
製造業に属するほぼ全ての業種を対象としています。
なお、支援対象の80%は、従業員規模30名~80名(パート含む)の工場です。
“カスヤ技術士事務所”は、なぜ中小製造業を支援しているのですか?
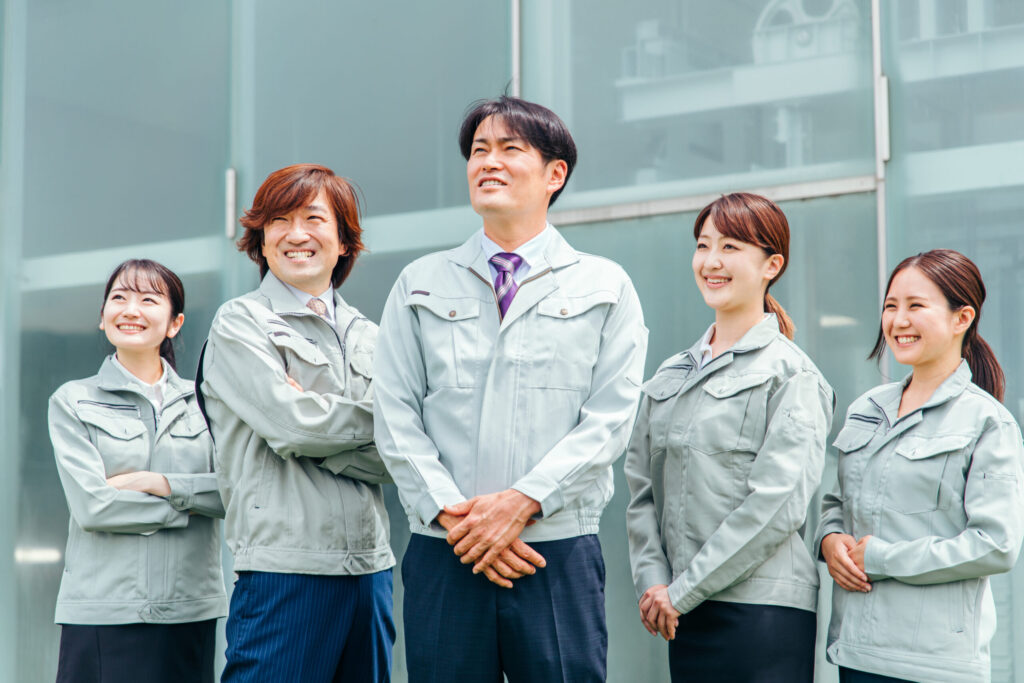
日本の中小製造業(従業員規模30名~80名)への本質的な支援が不足しているからです。結論から言うと、日本の中小製造業には外部の支援が絶対に必要です。
「作れば売れた」高度経済成長時代とは異なり、
現代は工場の生産性を徹底的に上げて利益を確保しないと生き残れない時代です。
しかも、顧客の値引き要求、経営者の高齢化による世代交代、
そして東アジア諸国との競争激化、といった厳しい経営環境の中、早急に手を打たなければ手遅れになりかねない状況です。
でも現実は、「このままではマズイ・・」と感じながらも、具体的に何をどうすればいいか分からない、
または自分たちでできることはやっているが成果が出ない、という工場が大多数なのです。
そんな危機的状況の中、
大手・中堅のコンサルティング会社に支援を依頼すると莫大な費用がかかります。一方で、費用のかからない行政の支援は、主に設備投資や運転資金の融資で、工場を本質的に改善する具体策は期待できません。結局、どちらも中小製造業には不向きなのです。
だからこそ、「日本の中小製造業を救うため、私達がやるしかない!」と決意し、中小製造業に特化した支援を行っているのです。
“カスヤ技術士事務所”は具体的に、どのように支援するのですか?
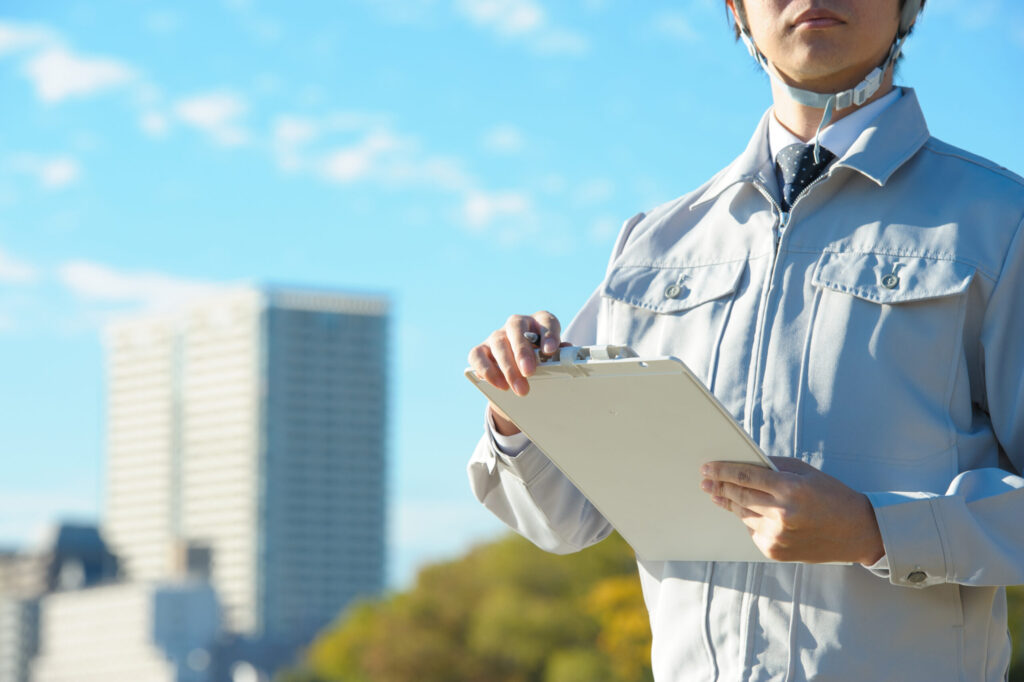
『工場学』という、どのような業種でも導入可能な『工場の生産性を30%向上するプログラム』を導入することで、工場の利益を増やします。
工場学の基礎からじっくり説明し、
工場の管理者・監督者と現場でいっしょに汗を流しながら、利益が出るしくみを構築していきます。
また工場改革が発展するときに必ずぶつかる課題を一緒に乗り越えて行きます。
従来のコンサルティング会社にありがちな、
机上の理論を振りかざし、お客様を煙に巻こうとする。工場改革が軌道に乗るまで丁寧に面倒を見てくれない。
客観的な立場からアドバイスするだけで、現場でいっしょに汗をかいてくれない。このような形式的なコンサルティングは、私達の指導とは最もかけ離れています。
分かりやすくてシンプルなノウハウやアドバイスを提供する。結果がでるまで徹底的にしつこく指導する。
現場・現物・現実の視点から経営者や管理・監督者、従業員の皆様の考え方から変えていく。これが私達のコンサルティングスタイルです。
マラソンで言えば、伴走者としてあなたといっしょになってゴールまで走り抜く。これは私達が最も大切にしていることです。
『工場学』とは、どのようなプログラムなのですか?
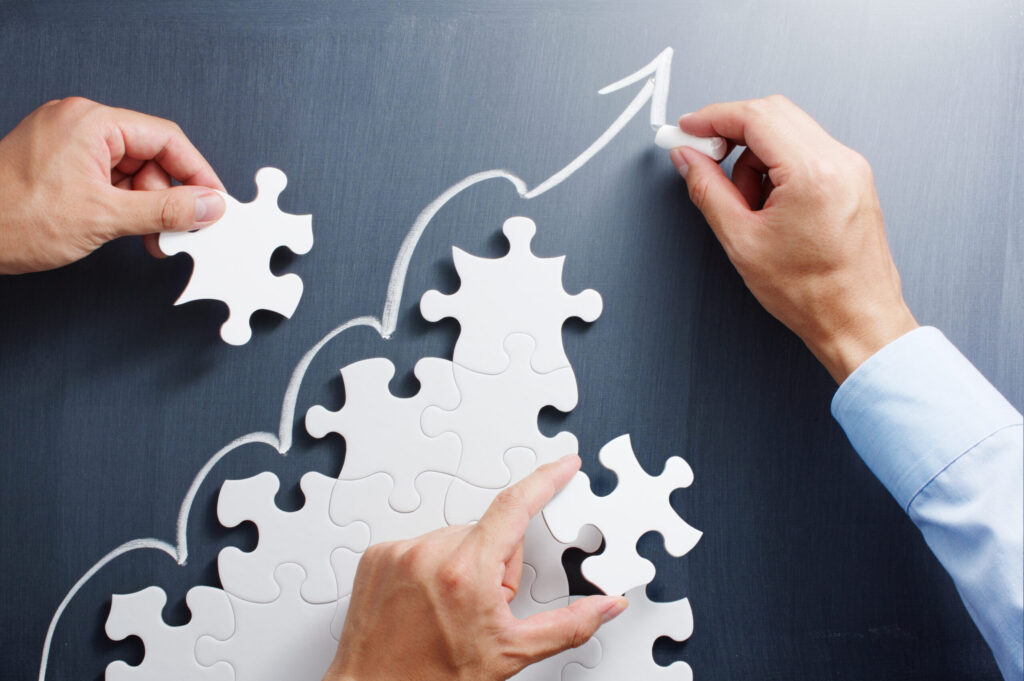
モノづくりの最高峰と呼ばれるトヨタ生産方式(TPS)を、自動車部品メーカー以外の中小製造業へ応用するために、
近江技術士事務所が独自開発したプログラム『FL 法』を
更に方法論だけではなく、クライアントの行動変容を最優先にすべく、行動経済学や脳科学の方法論を体系化したものが『工場学』です。
日刊工業新聞社から 11 冊の解説書(トヨタに学びたければトヨタを忘れろ シリーズ 著:近江堅一)
が出版され、28年間で480以上の中小製造業の工場に導入実績があります。
具体的には、お金をかけずに(設備投資しない、コンピュータシステム等導入しない)、工場の生産性を30%アップするプログラムで、どのような業種でも導入可能です。
中小製造業が、『工場学』を導入するきっかけは何ですか?
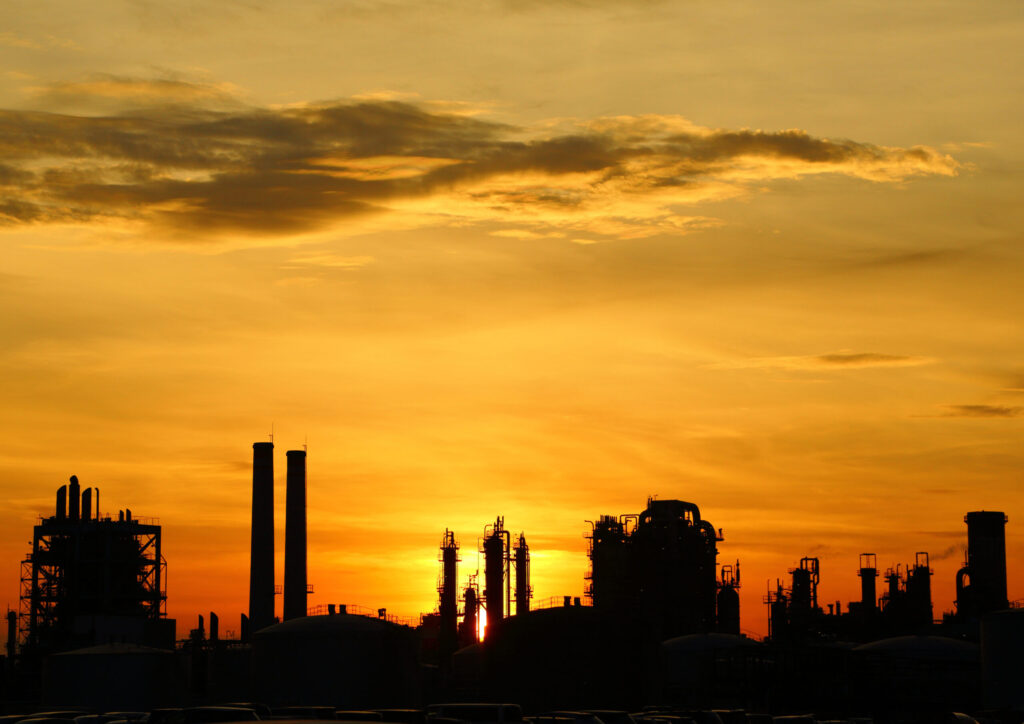
金属加工「顧客からの値引き要求により、赤字決算になったから」セラミック製品加工「売上減により、赤字決算になったから」
食品加工「材料費や人件費の高騰で、利益確保が厳しくなってきたから」縫製業「創業者の自分が引退する前に、工場管理を強化したかったから」精密部品加工「若い課長向けに、次世代管理者教育を行いたかったから」
プラスチック成形「日々、ムダが多いと感じていたところで、工場学を知ったから」印刷業「工場学で成功した工場が、当社の工場の状況とよく似ていたから」
『工場学』を導入した工場で、どのような効果が出ていますか?
『工場学』を導入するには、どうすればよいのですか?
まず、毎月開催しているセミナー参加頂きます。
その後、個別相談・工場診断を受けてもらい、工場学の導入方法を具体的に説明します。工場学の内容をしっかりご理解いただいた上で、導入するか、しないかを経営者様にご判断いただきます。
工場診断とは、御社工場へ伺い、現場を1時間ほど回りながら、工場の状況を確認することです。医者に例えるなら、精密検査になります。
最初の問診で、患者が「胃が痛い」と言えば、医者は「胃潰瘍の可能性がある」とは想像できますが、本当に胃潰瘍かどうかは分かりません。
もちろん胃カメラ等による精密検査が必要になります。
精密検査をし「写真を見るとここに異常がある、よって胃潰瘍で間違いない」という裏づけをとることで、やっと患者に納得してもらえます。
これと同様に、工場診断でその証拠を示します。
これで経営者様や従業員が「異常」を認識できるのです。
以上