【22社で成果実証済】3ヶ月で利益が上がり続けるしくみを作れる「ほったらかし経営」公開セミナー 令和7年1月20日開催
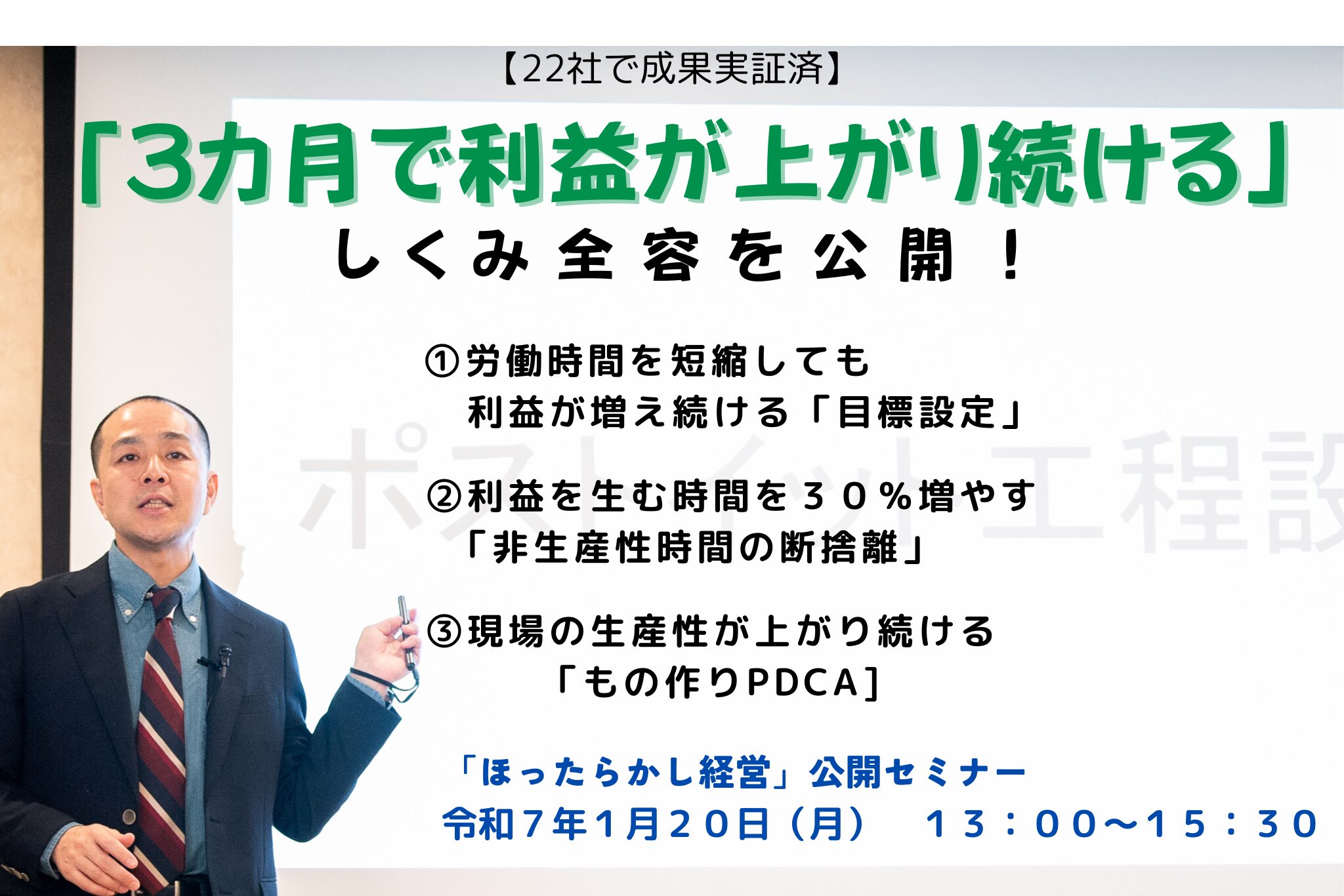
儲かる工場の
経営者が考える
『ほったらかし経営」
セミナーで
手に入るもの
3ヶ月で利益が
上がり続ける
しくみの全容
1労働時間を短縮しても
利益が増え続ける
「目標設定」
2利益を生む時間を
30%増やす
「非生産時間の断捨離」
3現場の生産性が
上がり続ける
「モノ作りPDCA」
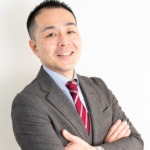
皆さん、こんにちは!
週休2日で利益率300%を
約束できる工場学
「ほったらかし経営」を
お伝えしている
糟谷(かすや)です
本セミナーでは、
これまで263回以上、
『お金をかけずに利益を上げる
中小製造業ならではの方法』
をお伝えしています!
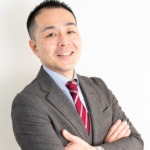
これまで、
多くの経営者様の
欲しい未来を
実現していきました!
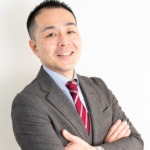
実際に皆さんと同じ様な
悩みを持っていた工場が、
工場学を取り入れたら
どうなったかということを
2つの実事例で紹介します
大阪府、板金加工工場、40名
コンサルティングに入る前に
経営者が最重要顧客の
購買担当者から言われた一言
「短納期対応してくれるなら、
海外には注文は出さないよ」
価格で海外工場に勝てないのなら、
短納期対応で勝負するしかない
しかし、かなり難しい要求に
どう対応したらいいか…
経営者は眠れない日々が
続いたと言っていました
今回お伝えする工場学の
3ステップがありますが、
実際この工場は、
コンサルティングを導入した結果
12か月で生産性は40%上がり、
この業界の常識では納期は2,3週間が、
なんとその常識を破り、
リードタイムは3,4日以内に短縮
更に、月当たり700万円の利益が
でる工場になったのです!
愛知県、金属加工工場、50名
コンサルティングに入る前は
顧客から衝撃的な
値引き要求がありました!
経営者は
「急に10%の値引きだなんて、
これからどうしていいものか…」
と悩んでいたのです!
実はこのメーカーの顧客は
親会社であり、
大手企業の子会社であっても
抜本的な改革をしなければ
生き残れない厳しい状況を
物語っているのです!
今回お伝えする工場学の
3ステップがありますが、
実際この工場は、
コンサルティングを導入した結果
9か月で生産性は33%上がり、
月当たり500万円の利益がでる
値引きされても利益を生み出せる
工場に生まれ変わったのです!
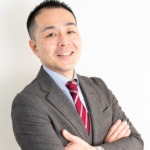
皆さん、更に、こんな
お悩みはありますか?
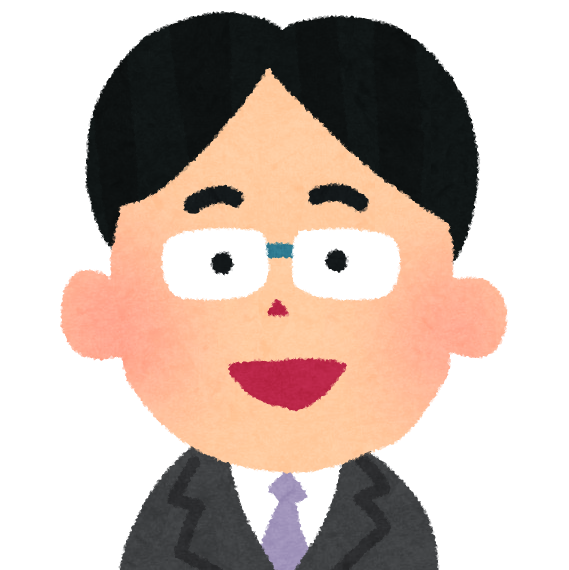
納期対応に追われ、
毎日残業し、休みもない!
このままでは、
工場が潰れてしまう!
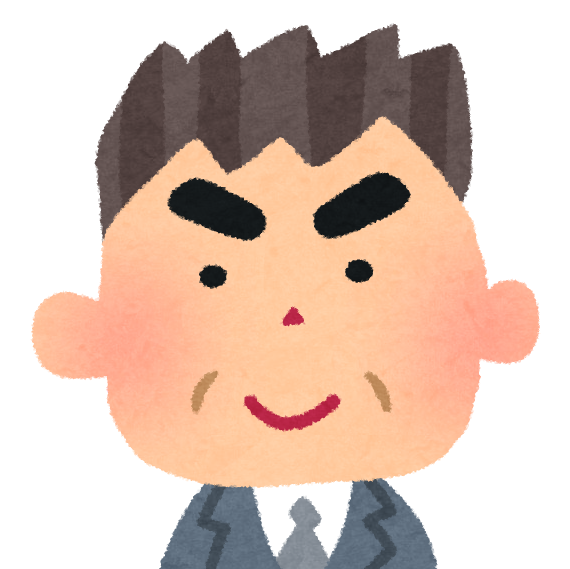
皆、忙しそうにしている
割には、利益が少ない!
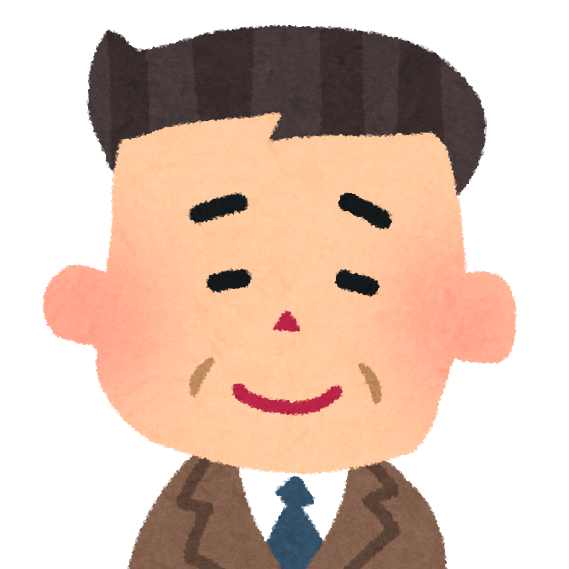
工場は、休みなく
働いている!
残業をなくして、
週休2日は与えたい!
それでも黒字化したい!
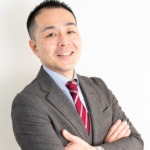
そんなあなたに朗報です!
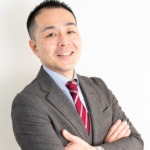
令和6年8回実施し、
とにかく好評でした!
これは、もっと多くの
経営者に伝えたいと思い、
アップデートした内容で
実施します!
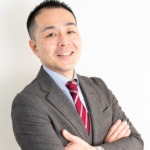
皆さん、工場を
一生懸命に経営しようと
考えてはいけません
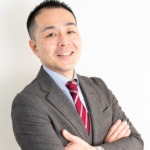
工場経営こそ
「ほったらかし」で経営
しなければならない。
「ほったらかし」で経営
することが重要なのです
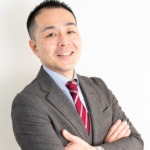
つまり、
利益を増やしたい、
黒字経営にしたいので
あれば「ほったらかし」にしましょう!
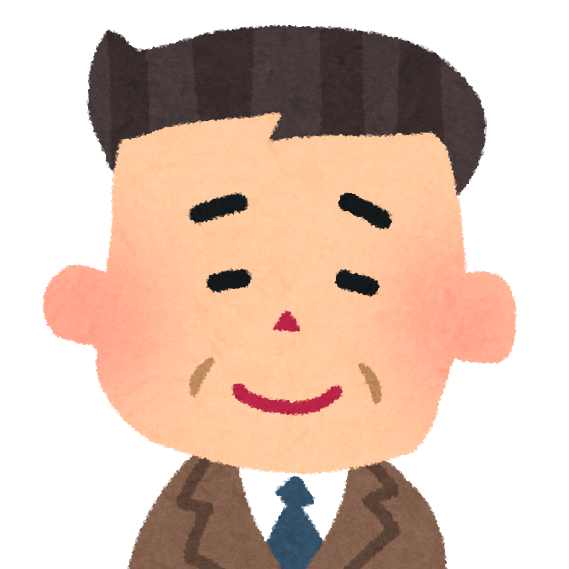
「ほったらかし」
にするとは、
どういうことか?
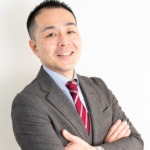
ほったらかしにしても
大丈夫な「しくみ」を
作ることです。
何もしないでもよいという
ことではありません!
儲かる工場のほったらかし経営とは
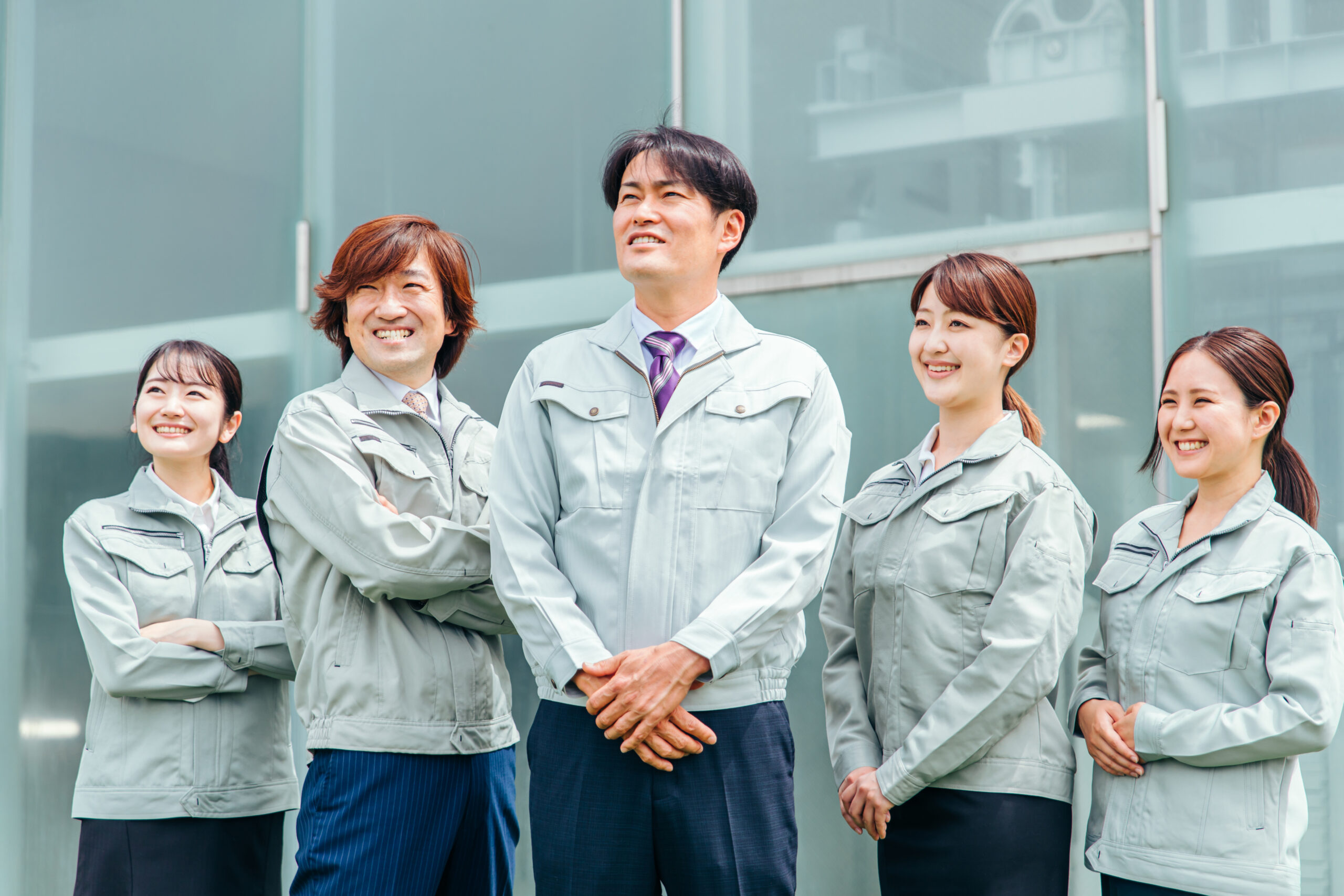
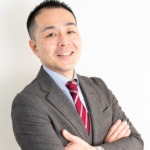
ムダなものを省いて、
生産に必要なだけの
しくみをつくれば、
後は、そのしくみが
勝手に働いてくれます
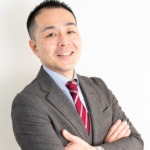
このしくみをつくれば、
ほったらかし経営の完成!
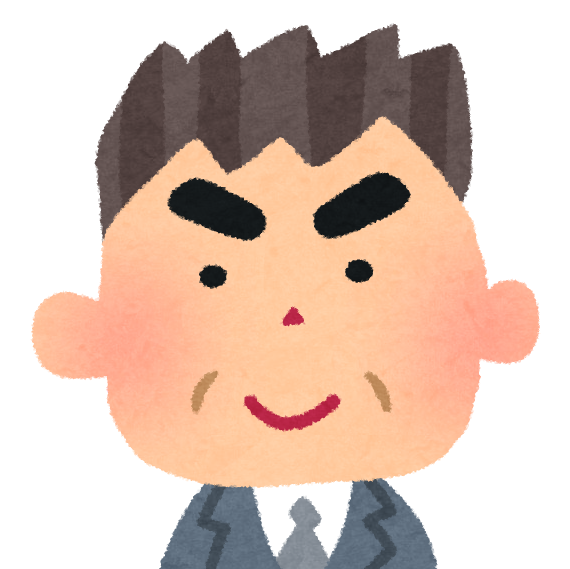
では、
ほったらかし経営をせず
経営をほったらかしに
するとどうなるか?
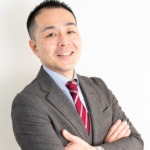
当然、
赤字経営になります。
工場はムダだらけです
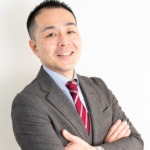
でも、あなたが、
ほったらかしにしたい、
できれば楽をしたい、
難しいことは考えたく
ない、それは正解です。
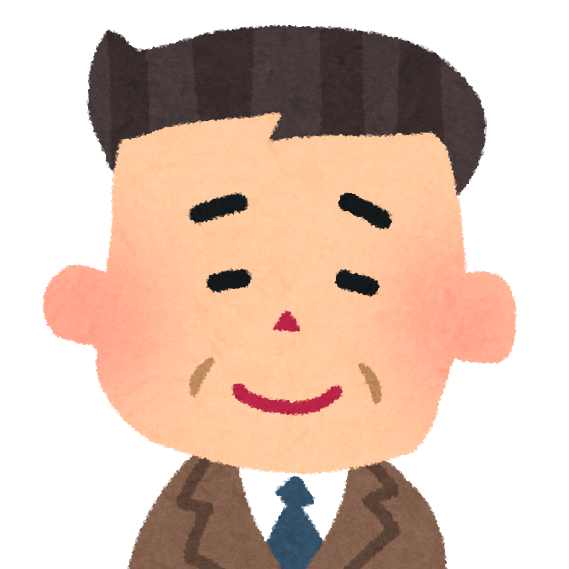
だから、
ほったらかし経営をしたら
いいということですね!
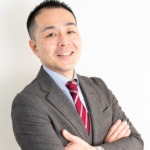
はい、しかし、
その状態にするためには、
ほったらかしにしてもいい
しくみをつくらなければ
ならないです。
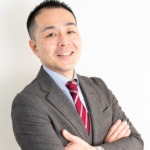
これが、
私がお伝えしている
「ほったらかし経営」の
本質です。
ほったらかし経営にするための「工場学」
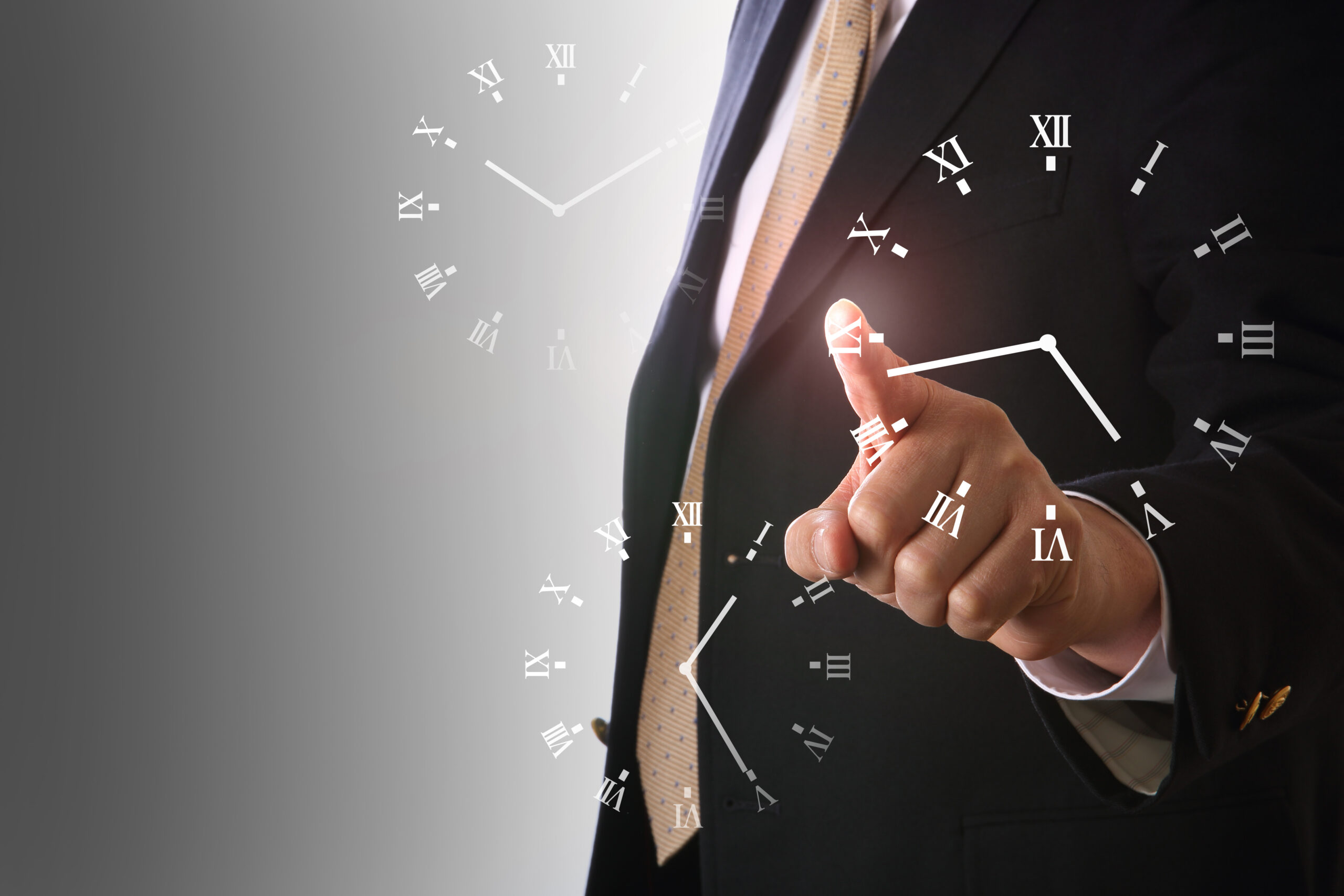
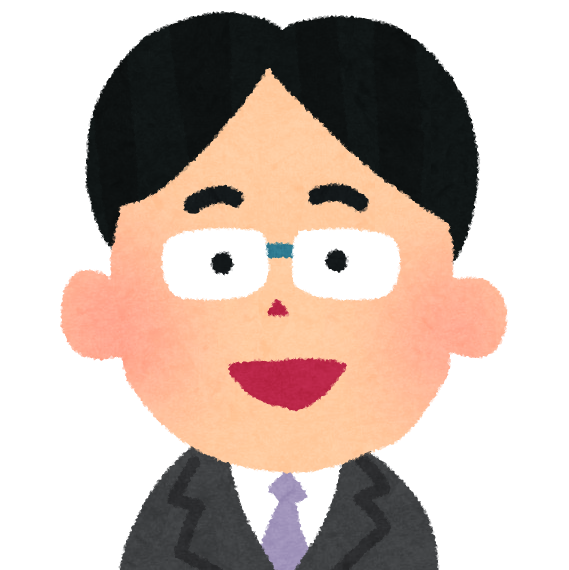
では、
ほったらかし経営を
するためには?
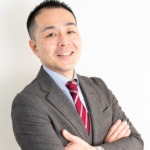
「工場学」というものを
知らなければならない!
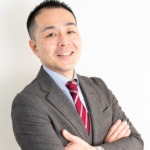
工場学を知れば、
ほったらかし経営が
できて、
利益率が向上し、
黒字化経営ができます!
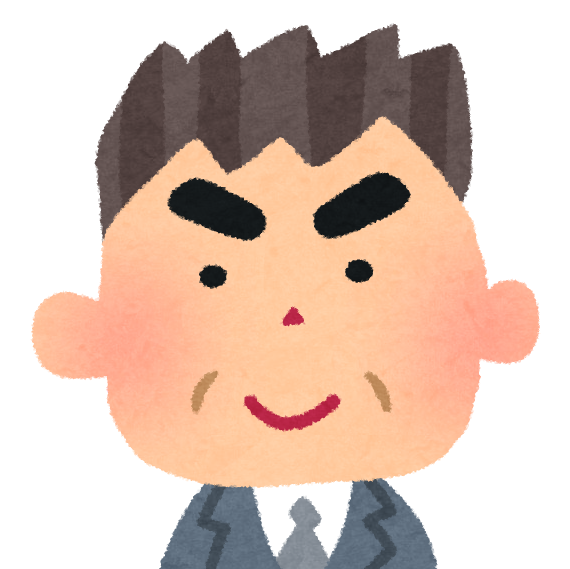
工場学?!
聞いたことないですね
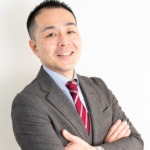
そうですよね!
私が作った『造語』です!
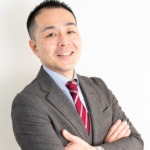
今回の特別セミナーでは、
工場学について
お伝えします。
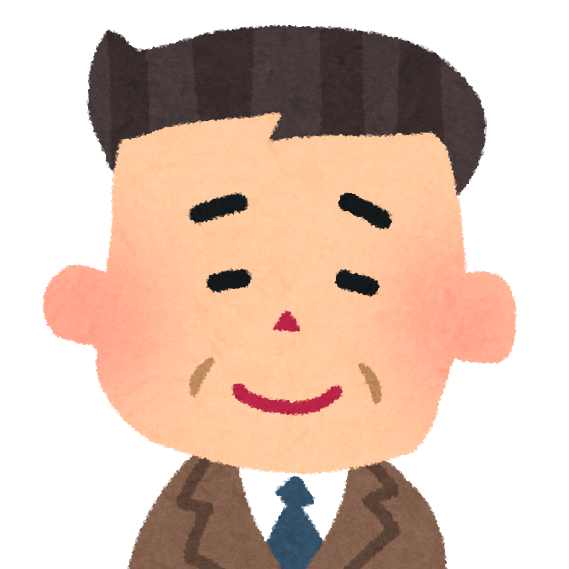
それは楽しみです!
はじめて聞く言葉です!
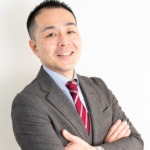
工場学を学べば、
あなたの工場に
工場学を取り入れることが
できます!
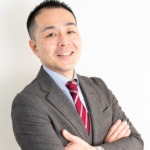
つまり、
工場学を取り入れる
ことができれば、
ほったらかし経営が
できるのです!
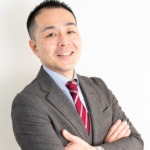
これから、
あなたに必要なものは
工場学です!
これらは、ほんの一例です!
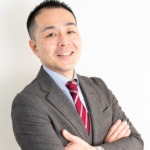
私は、
これまで29年間で
490工場の黒字化をした
FL法を『工場学』へと
アップデートし、
46社工場の利益率を
向上させてきました
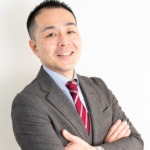
なぜ、そのような成果を
出すことができるのか?
それは、
工場学という考え方を
取り入れてきたからです
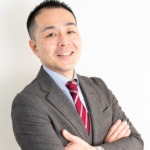
この特別セミナーで、
「ほったらかし経営」
を実現するための、
工場学を
手に入れてください!
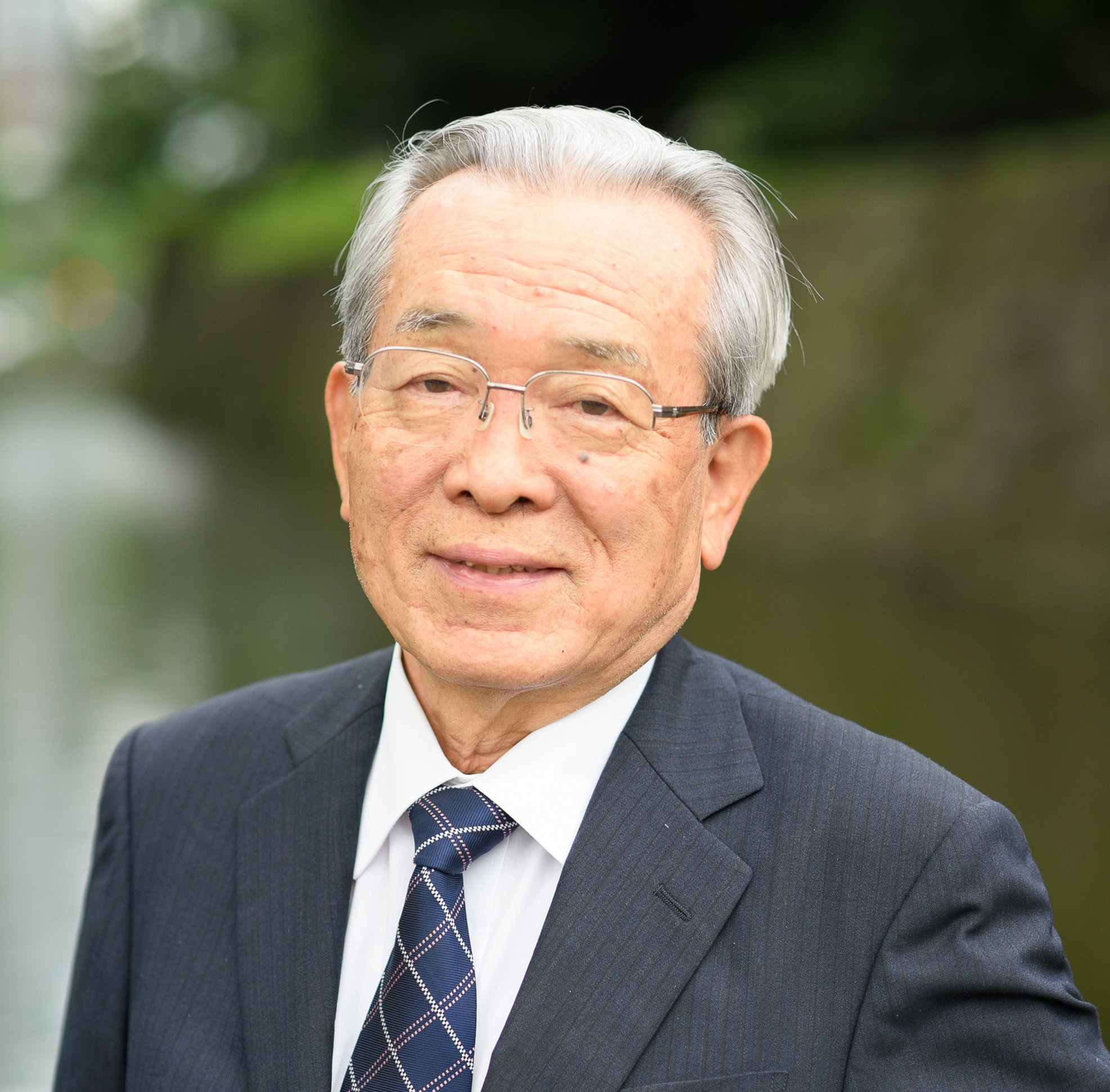
私の『中小製造業向け
トヨタ生産方式』を継承
した、糟谷さんによる
【工場学】!必見です!
セミナー後に指導させていただいた
成形工場では、わずか185日で、
定時操業(残業0時間)
完全週休2日、400万円/月の黒字化
に成功!
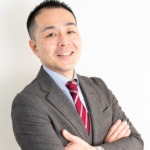
近江先生、
ありがとうございます!
工場学は必須です!
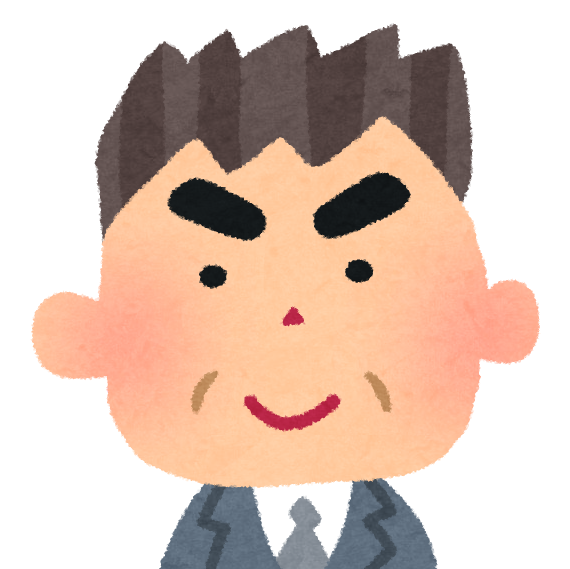
なるほど。
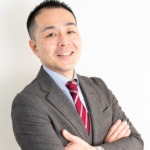
令和7年こそ、
工場を最高の状況に
したい!だったら、
この1月は、
工場学を導入して
工場改革するチャンス!
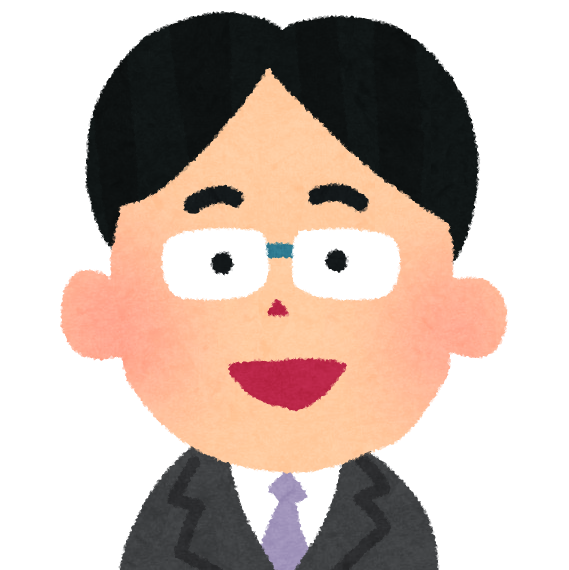
そうですね!
開始するには
良いタイミングですね。
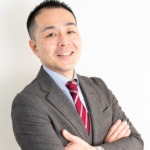
あなたの工場の
現状把握をして、
工場の『どこを、
どうすればいいか』を
しっかりとお伝えしますね!
時間活用の『しくみ』を作るだけ!たった185日で4割の生産性向上
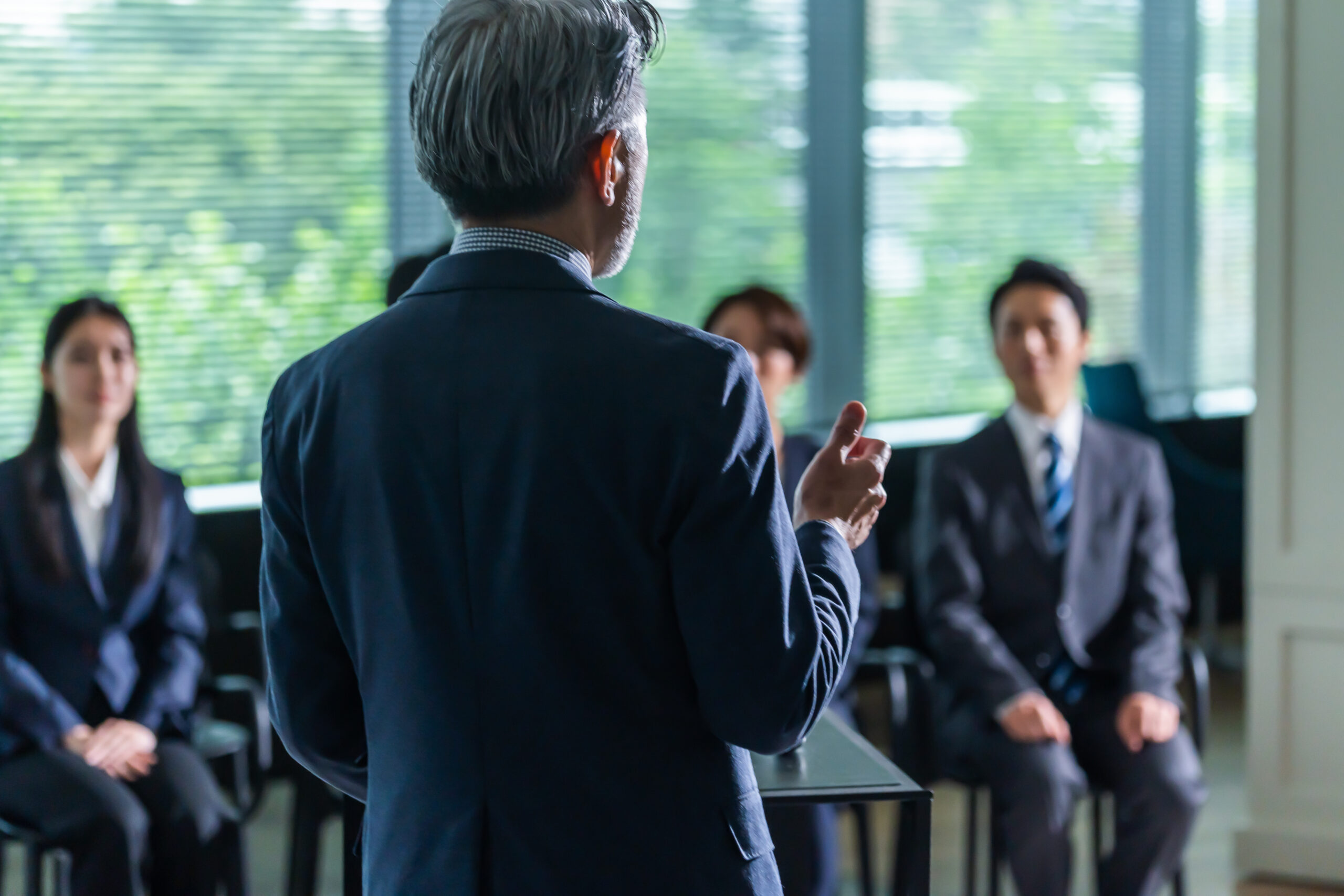
日時:
1/20(月) 13時 ~ 15時30分
費用:
・超早割お申込み 1/10 – 13:5,000円
・早割お申込み 1/14 – 15:7,000円
・一般お申込み 1/16 – 17:10,000円
定員:経営者様 5社限定
参加方法:Zoom(オンライン)のみ
※URLをメールでご連絡します
主な内容:
・工場が良い仕事をした
尺度を決める
・作業者に時間を入れた
作業指示をだす
・現場リーダーはラインからはなれ、
作業者の進捗管理をする
・全受注に対し、工程毎に段取時間
と加工時間を入れた工程設計する
・『12歳の法則』を公開!
工場が利益を生みだすためには、
単に頭で理解して行動を起こせば
いいというわけではありません
講師:
糟谷 徹 技術士(経営工学)
これまでの18年間、
大手製造業と中小製造業の
現場を研究開発から工程設計、
海外工場の立ち上げから、
品質管理までを実務で経験し、
製造現場を熟知
29年間で490工場を黒字化した
FL法を工場学へとアップデートし、
令和6年まで46社の工場の利益率を
向上させ経営者から喜ばれている
利益が継続するしくみが
できるまで手厚いサポート!
これまでの実績は、
22社が3ヶ月でしくみが完成
●機械加工工場 赤字
⇒しくみ構築後、
月600万円の黒字化
●板金加工工場 赤字
⇒しくみ構築後、
月500万円の黒字化
など売上貢献額は合計20億円を超え
コンサルティングをしてきた
46社(※令和6年までの実績)の
平均では6ヶ月でしくみを完成させる
業界では異例の
再現性とスピードを誇る
コンサルティングをしている
【特典】利益を生みだす秘訣や改善リーダーの育成法、無料個別相談
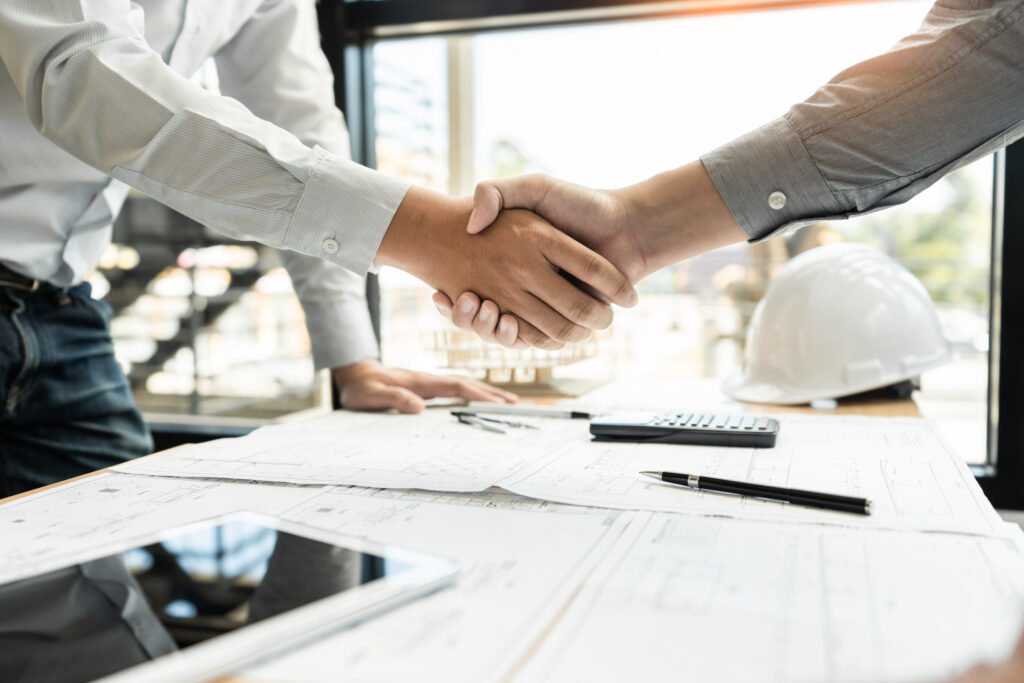
特典:
・先着 3名:A、B を特別プレゼント
・先着 5名:B を特別プレゼント
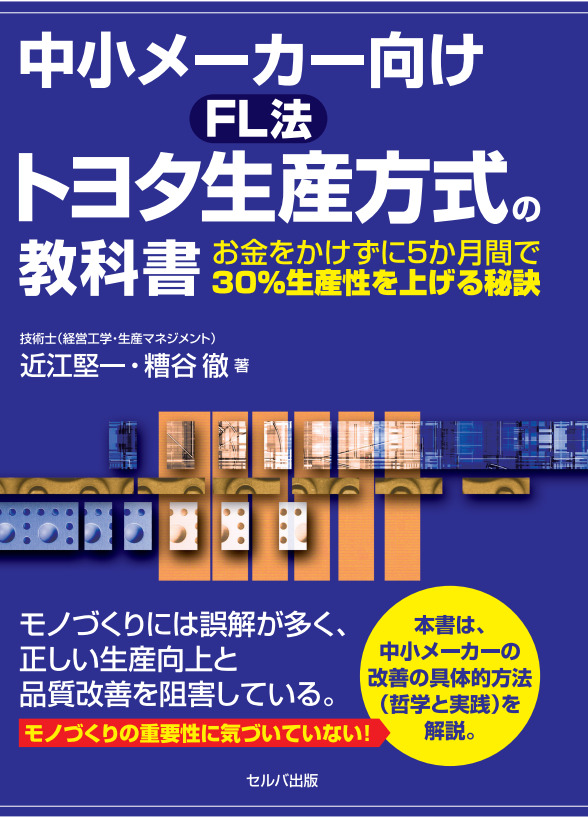
特典A:
中小メーカー向け
トヨタ生産方式(FL法)
の教科書
(近江堅一、糟谷徹 著)
※2023年11月発売の新刊!
増版感謝特別プレゼント!
中小メーカーの改善の
具体的な方法【哲学と実践】
が手に入る!
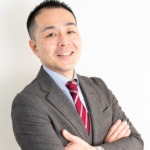
ぜひ、お読みください!
効果を実感してください!
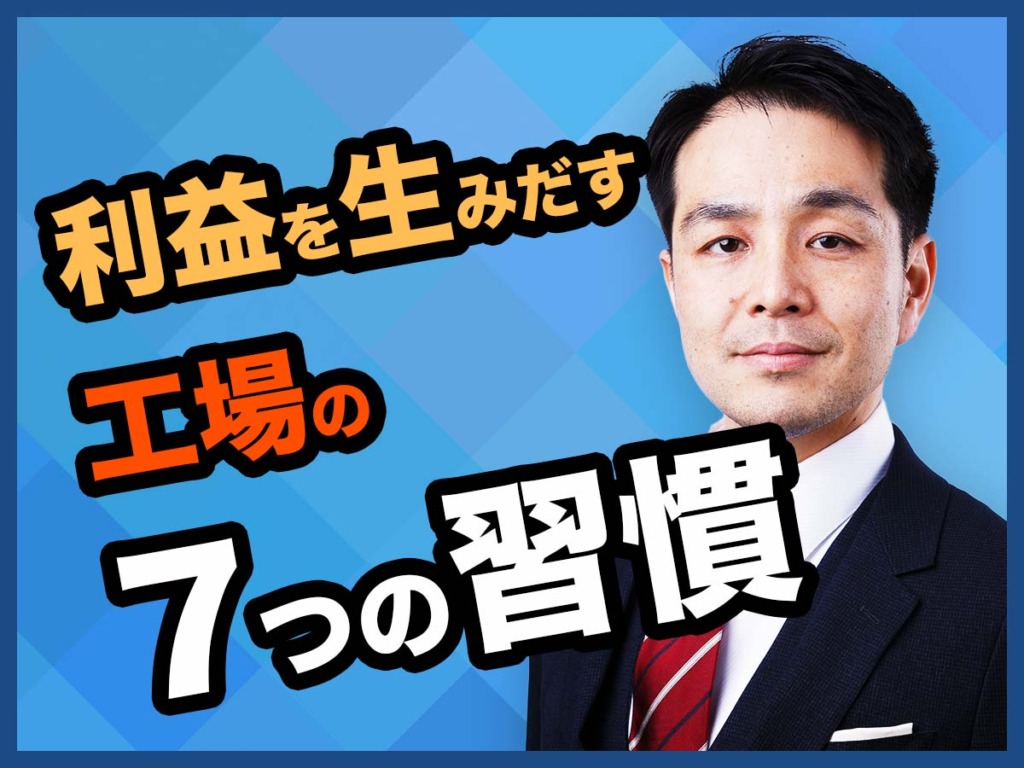
特典B:
利益を生みだす7つの習慣
糟谷がお届けする特別レポート
⇒たった7つの習慣を実践するだけで
利益を生む最強の習慣が手に入る
なぜ『今』工場改革を進めなければならないのか?
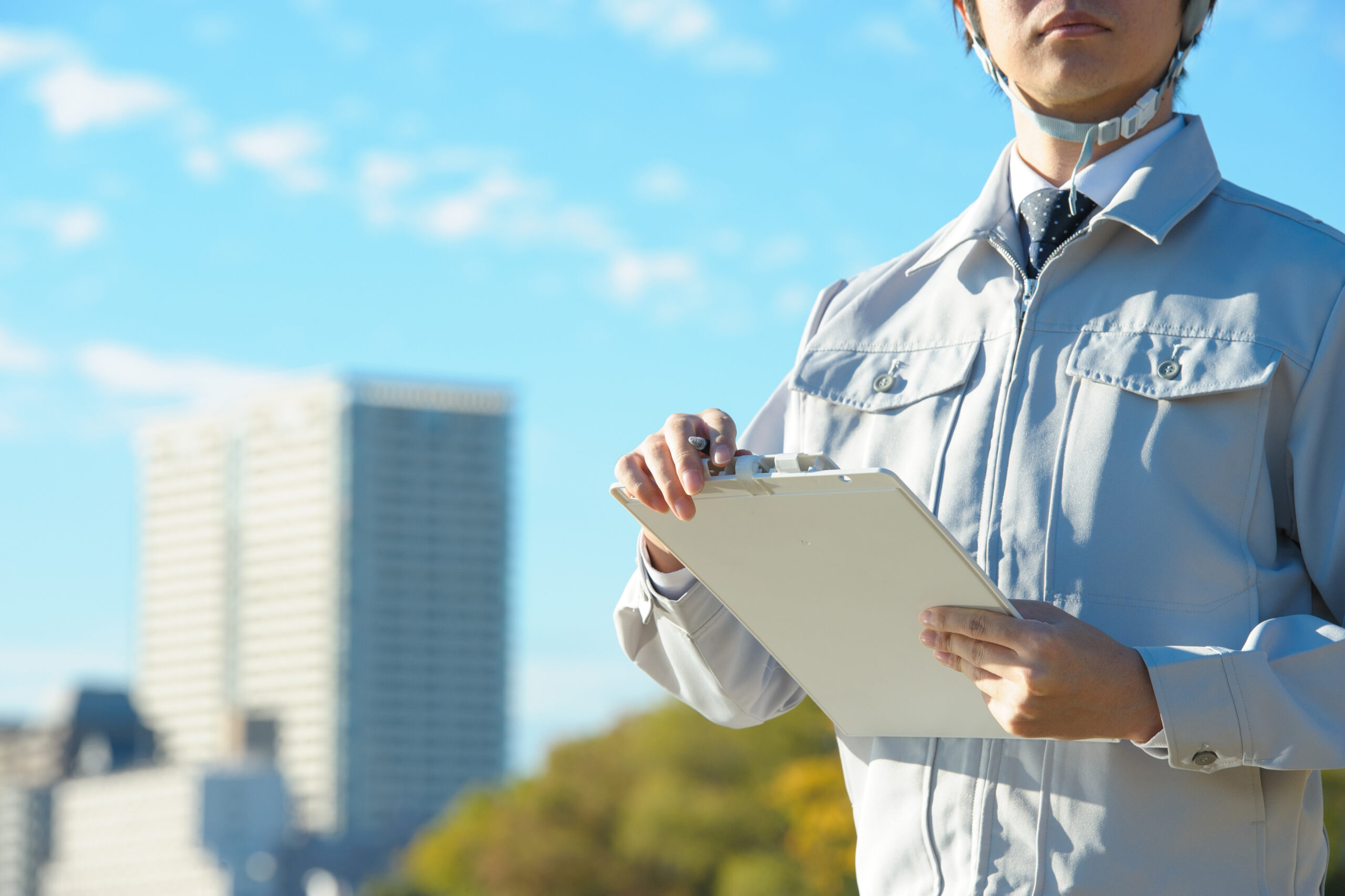
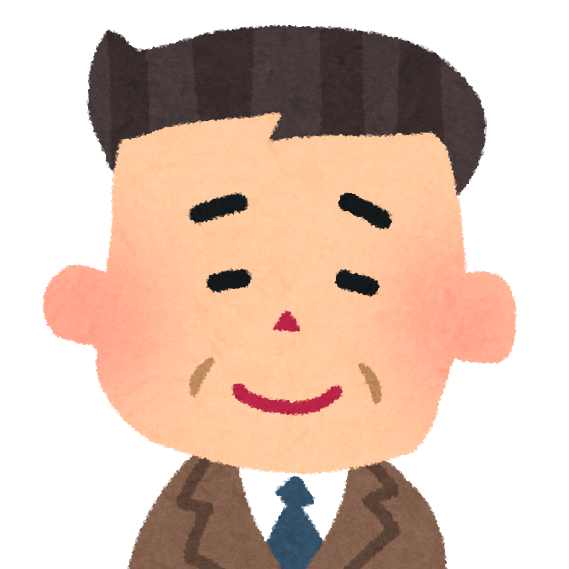
でも…なぜ『今』
工場改革を進めなければ
ならないのでしょうか?
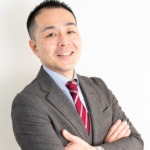
それは、良い質問です!
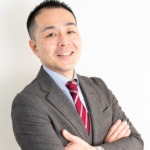
日本の製造業は、
これから将来を見据えて、
『強い工場』に生まれ
変わらなければなりません
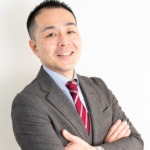
私の言う『強い工場』
というのは、受注が減って
も確実に利益を生み出す
ことができる工場です!
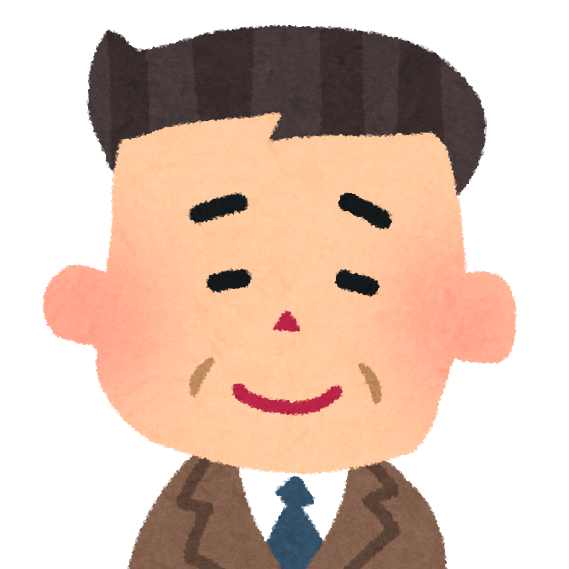
強い工場ですか!
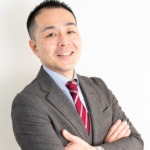
はい、受注が多ければ、
どんな工場管理をしても、
利益が出てしまうんです。
特に大ロットのリピート品
があれば、例えムダだらけ
でも利益が出てしまいます
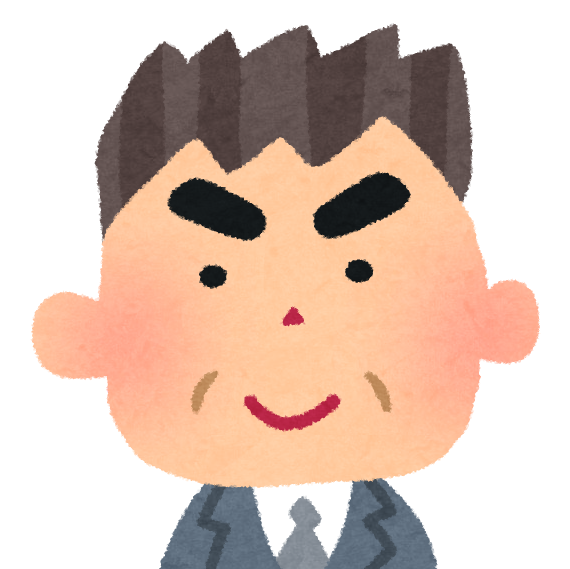
確かに、そうだね
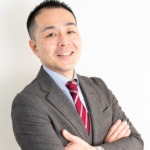
では、想像してください。
受注形態が変わることは
よくありますよね。
また受注量が減ると、
途端に利益が減少し、
最悪、赤字決算に転落して
しまうケースも
少なくありません。
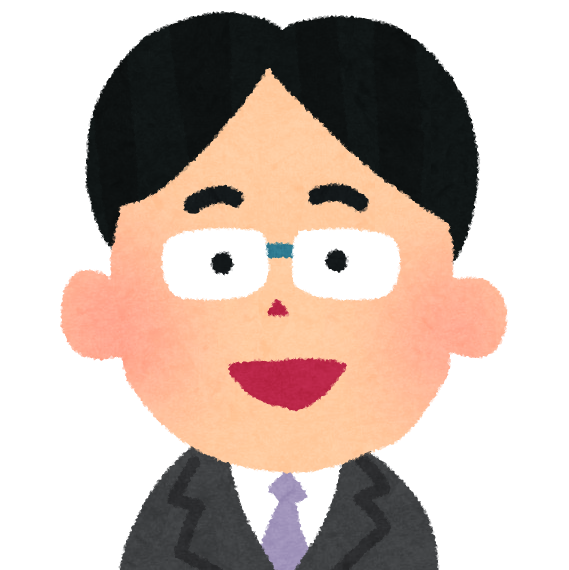
うちは、コロナ以降、
受注量が減っている!
受注形態だって、
大ロットから、小ロットを
要求されているんです!
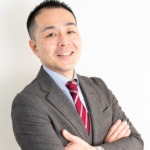
もちろん、売上が
右肩上がりならよいです。
しかし、永遠に売上が
右肩上がりに続く企業
なんてあり得ません!
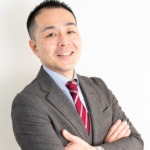
どこかのタイミングで、
必ず工場管理を強化
しなければならない!
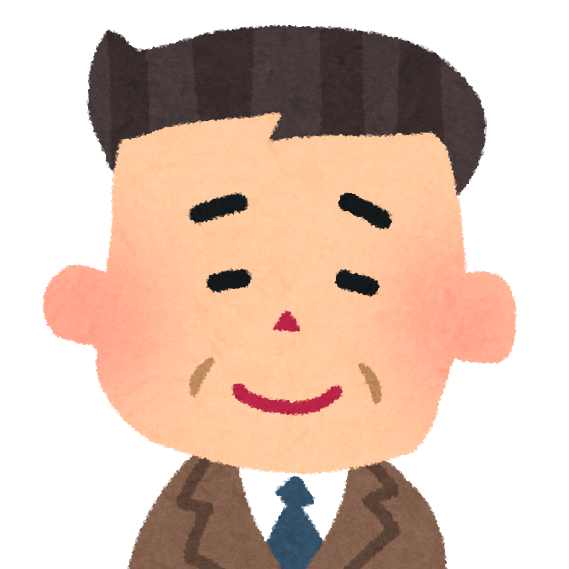
つまり、工場管理を
強化するタイミングは
『今』なんですね!
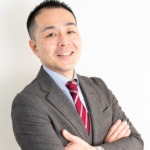
はい、その通りです。
一番いいタイミングは
『今』です!
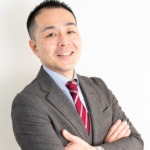
理由は、問題点に早く
気づくことができるから。
問題点に早く気づくことが
できれば、対策が早く
打てますよね!
だから『強い工場』に
生まれ変わるのも
早くなるんです!
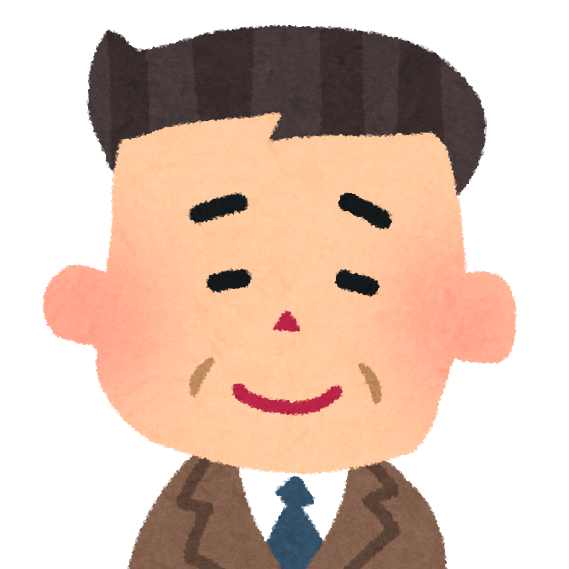
そうですね、
まだ余裕がある
『今』のうちに、
工場改革を進めて
おきたいですね。
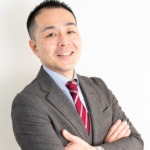
それは素晴らしいですね!
一緒にがんばりましょう!
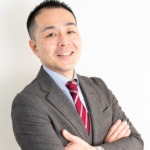
最後まで読んでいただき
ありがとうございました。
今こそ、
工場管理を
強化してみませんか?
参加申し込み、
お待ちしております。
コメント