改善力を身に付けるために管理者に知ってほしい発想法とは?
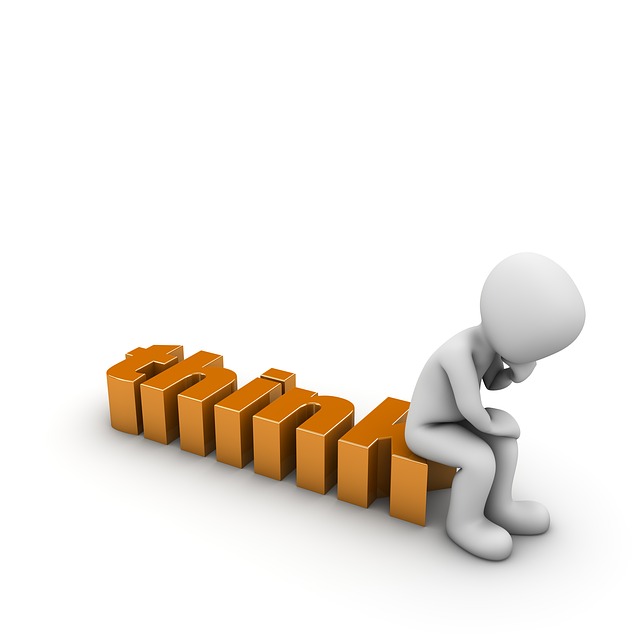
こんにちは、技術士(経営工学)のカスヤです。
工場の生産性向上指導を通して、
強く感じることは、
工場改善を推進する
強いリーダーが不足している
ということです。
そこで、
改善力を身に付けるために
管理者に
知ってほしい発想法を解説します。
本日から数回にわたり、
自ら改善リーダーになるために、
どのような考え方・発想を持てばよいかを
徹底解説していきます。
一見、
常識と反する内容と思えるかもしれません。
しかし、
一旦素直に受け入れて実施して頂ければ、
必ず成果が出ます。
前回までに紹介した発想法の復習
↓↓
改善力を身に付けるために管理者に
知ってほしい発想法とは?続
それでは、いってみましょう。
改善力を身に付けるために管理者に知ってほしい発想法「製造条件を見直せ」
前回話した、
段取時間の短縮は
リードタイムの短縮に
大きく貢献します。
そして、本日のテーマである、
製造条件もリードタイム短縮の
視点から検討します。
改善リーダーであるあなたは、
製造条件を見直したことがありますか?
ほとんどの人は、
最初に決められた製造条件を
見直そうとはしません。
これは大きな盲点です。
改善リーダーには
是非気付いてほしいものです。
具体的に考えてみましょう。
熱処理速度が20cm/minと決められているとします。
また乾燥時間は100℃で3時間とします。
多くの場合、
20cm/minは初期段階(試作検討時)では、
この速度であれば、
特性の保証上問題はない、
という観点で決められ、
現在もそのままの速度で
作業が行われています。
したがって、
初期段階ではリードタイムを短くしよう!
という観点からは検討されていません。
今後は、この観点から速度は
どこまで上げてよいかを
検討する必要があります。
この例では、
22cm/mmで問題ないことが確認され、
乾燥時間も100℃で2時間で
問題ないことが確認されました。
このように、
製造条件を初期段階で決めるとき、
限られた時間内で
特性保証面を主体に検討し、
リードタイムを短くする
観点から決められていません。
よって、
リードタイムを短くする観点から
現在の製造条件を総点検してみて下さい。
管理者であるあなたは
ここに気づいていましたか?
気付かないのは、
リードタイム短縮の価値認識がないからです。
改善力を身に付けるために管理者に知ってほしい発想法「ネック工程前の置場を管理せよ」
改善リーダーであるあなたは、
ネック工程を認識していますか?
ネック工程とは、
一番能力のない工程になります。
だから、
ネック工程の置場には
必ず加工するものが
置かれていなければならない。
しかし、
ネック工程が消化する
以上のものを置いても
ムダになります。
そして、
これを実現する方法が
ネック工程前の置場管理です。
具体的に説明しましょう。
例えばこの置場には、
ネック工程が加工する
2時間分+2時間分が置いてあります。
ネック工程が加工を始めて、
残りが2時間分になったら、
ネック工程の前工程には
2時間分の製造を行います。
この2時間分の加工が終わるまでに
他方の2時間分が補給されているので、
ネック工程で加工するものが
欠品することはありません。
この例は、
発注点が2時間分で、
発注量が2時間分に
相当する補充方式です。
これは、
ネック工程の置場が
前工程へ生産指示を出す
しくみになります。
また、
生産停止情報を発信するしくみとしても、
置場管理のやり方は有効です。
なぜなら、
トラブルが発生した際、
生産停止情報が機能しないと、
必要以上に仕掛品を作ってしまいますよね。
具体的に説明しましょう。
各工程間に
「次着手品置場」を作り、
「次着手品置場」が一杯になり、
ものを置くことができなくなった場合には、
生産を止めるというものです。
非常に簡単かつ極めて有効な手段です。
お試しください。
旧ブログはこちらからどうぞ。
http://pe-michanpapa.hatenablog.com/