【工場学】8割の工場が勘違い!利益が出ず継続もしない間違った5Sとは!?
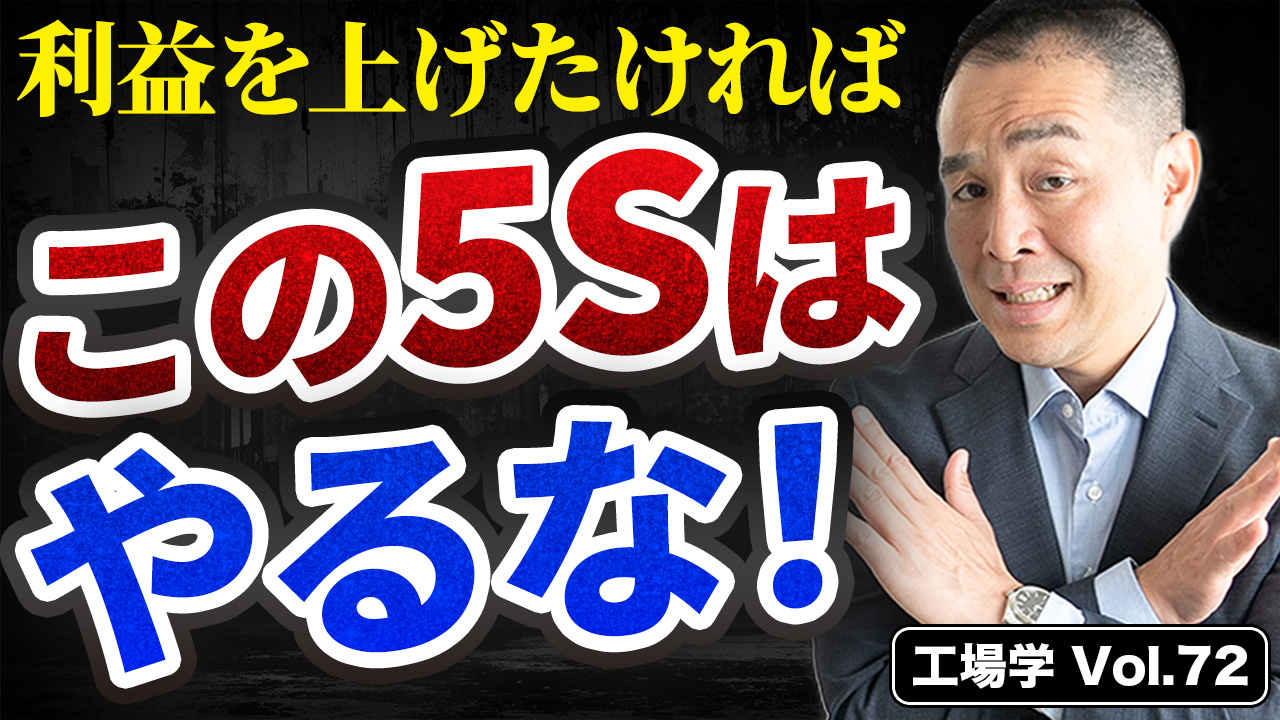
🔍 5S活動の課題
多くの工場で5Sが一時的な取り組みで終わってしまい、定着しない。
💡 精神論の限界
「掃除=5S」と誤解されがちで、精神論だけでは継続しない。
📉 属人化の危険性
活動が個人のモチベーション任せになると、自然消滅してしまう。
📊 科学的アプローチの必要性
5Sを定着させるには、現状をデータで把握・管理する仕組みが不可欠。
🧠 「対象」と「観点」の導入
経験や勘に頼らず、5Sを標準化するためのフレームとして「対象」と「観点」が重要。
🧱 整頓の4レベル
整頓の成熟度を4段階(レベル0〜3)で定義することで、改善点が明確になる。
🏷️ 整頓レベルの例
レベル1:グループ化・識別管理
レベル2:ラベルによる情報可視化
レベル3:形跡管理で即座に把握可能に
📋 チェックリストの活用
整頓レベルをチェックリストで可視化し、改善目標を設定する。
🔧 ドリル整頓の改善事例
感覚的な整頓から実用性・安全性を加味した改善へ進化。
🧰 整頓の最適化視点
整頓は使いやすさを追求する“最適化問題”。人により得手不得手があるため、仕組み化が重要。
🎯 行動指針の提案
「整頓チェックリスト」を活用することで、誰でも実践可能な5Sが実現できる。
🚀 本質を学ぶ意義
物作りの本質に向き合うことで、継続的改善と利益率アップが可能に。
5S特に「整頓」のしくみづくりについて解説しました。
5S活動を「しくみ化」させて、コストダウンや生産性向上につなげて行きましょう!
コメント