強い工場になる5ステップ(ステップ5 現場改善の推進)
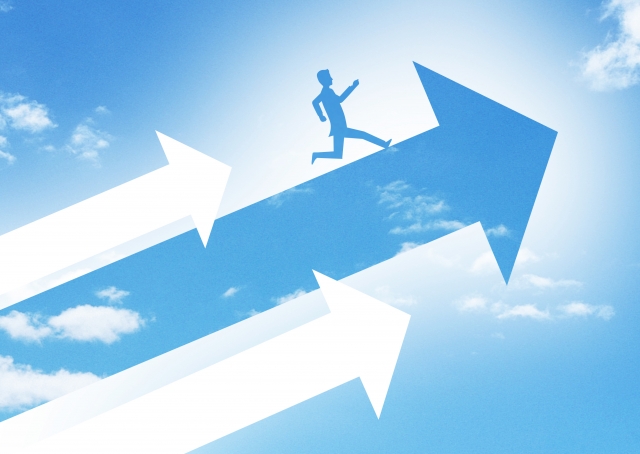
こんにちは、技術士(経営工学)のカスヤです。
「うちの会社(工場)は特殊だからな…」あなたも、聞いたことがあるでしょ?
でも、特殊な会社(工場)は存在しませんからね。
「どこの会社(工場)も問題の本質は同じである」ということなんです。
そして、連日紹介している「5ステップ」はどの業種の工場でも適応できるんです。
あなたの工場に当てはめて、読んで下さいね。
ステップ1「工場改革チームを立上げよう、リーダーは任せて育てよ」です。
ステップ2「生産性を上げる目標を設定せよ、目標は①期限と②目標値を含めよ」です。
ステップ3「現状把握は事実と意見を区別せよ、視点は情報の流れとものの流れ」です。
ステップ4「生産管理を強化せよ、必要なものを必要な工数でつくる」です。
本日からステップ5です。
さてさて、生産管理を強化できたら、いよいよ現場改善に入ります。
このステップ5はめちゃめちゃ重要ですので、頑張ってついてきて下さいね。
「時間短縮」「少人化」を重視せよ
現場改善というと、テーマは沢山あります。
まずは、「時間短縮」と「少人化」を重視して下さい。
では、「時間短縮」から行きましょう。
人が行う作業を想像して下さい。
「準備作業、清掃作業、段取替え、機械セット、組立作業、検査作業、梱包作業…等」
まずは、人が行う作業の時間を徹底的に短縮しましょう。
時間短縮は原則として半減を目指していきます。
例えば、段取替えに60分かかっているとしましょう。
この場合、まず30分にするという目標を立てましょう。
次に30分に短縮された場合は、15分という目標を立ててさらに改善するわけです。
そして、最終的には10分以内でできるように改善を続けます。
いわゆる、シングル段取りってやつですね。
ここで、段取替え短縮の簡単で効果が出るやり方をご紹介しておきますね。
まず現在の段取替え時間をストップウォッチで測定してみて下さい。
これだけで、段取時間は約3割短くなりますから。
そしてこの次は、外段取り化です。
例えば、次に交換する金型を前もって近くに置いておくことで、約2割は短縮できるんです。
どうでしょうか、これならすぐできそうでしょ。
さて、次は少人化ですが、次回解説しますね。
お楽しみに。
旧ブログはこちらからどうぞ。
http://pe-michanpapa.hatenablog.com/